System and method for directly reducing laterite-nickel ore through hydrogen shaft furnace dry-method self-reforming
A technology of laterite nickel ore and shaft furnace, which is applied in the field of laterite nickel ore smelting, can solve the problems of low production efficiency of direct reduced iron, low methane cracking rate, poor catalytic effect, etc., so as to avoid catalyst deactivation, improve smelting efficiency, clean production effect
- Summary
- Abstract
- Description
- Claims
- Application Information
AI Technical Summary
Problems solved by technology
Method used
Image
Examples
Embodiment 1
[0049] Use natural gas as the reducing gas. After desulfurization, the natural gas is sent into the heating furnace and heated to 1050°C. Then enter the hydrogen shaft furnace through the hot reducing gas inlet in the middle of the hydrogen shaft furnace. The laterite nickel ore oxidized pellets are fed into the receiving hopper on the top of the hydrogen shaft furnace. Wherein, in the laterite nickel ore oxidized pellets, the mass content of nickel is 0.8%, and the mass content of iron is 35%. After thermal reduction, it enters the hydrogen shaft furnace, under the condition of iron and nickel as the catalyst, through cracking and self-reforming reaction, the synthetic reducing gas is produced, in which H 2 And the volume fraction of CO is 93%. and H 2 / CO is 1.6. Synthetic reducing gas moves upwards, heats and reduces the laterite nickel ore oxide pellets moving from top to bottom in the upper part of the hydrogen shaft furnace, and the reduction time is 4 hours. In th...
Embodiment 2
[0051] Use natural gas as the reducing gas. After desulfurization, the natural gas enters the heating furnace and is heated to 1050°C. Then enter the hydrogen shaft furnace through the hot reducing gas inlet in the middle of the hydrogen shaft furnace. The laterite nickel ore oxidized pellets are fed into the receiving hopper on the top of the hydrogen shaft furnace. Wherein, in the laterite nickel ore oxidized pellets, the mass content of nickel is 1.7%, and the mass content of iron is 20%. After the hot reducing gas enters the hydrogen shaft furnace, under the condition of iron and nickel as the catalyst, the synthetic reducing gas is produced through cracking and self-reforming reactions, in which H 2 And the volume fraction of CO is 95%. and H 2 / CO is 1.6. The synthetic reducing gas moves upwards, heats and reduces the laterite nickel ore oxide pellets moving from top to bottom in the upper part of the hydrogen shaft furnace, and the reduction time is 2 hours. In th...
Embodiment 3
[0053] Coke oven gas is selected as the reducing gas. The coke oven gas enters the heating furnace after desulfurization and is heated to 950°C. Then enter the hydrogen shaft furnace through the hot reducing gas inlet in the middle of the hydrogen shaft furnace. The laterite nickel ore oxidized pellets are fed into the receiving hopper on the top of the hydrogen shaft furnace. Wherein, in the laterite nickel ore oxidized pellets, the mass content of nickel is 1.7%, and the mass content of iron is 20%. After the hot reducing gas enters the hydrogen shaft furnace, under the condition of iron and nickel as the catalyst, the synthetic reducing gas is produced through cracking and self-reforming reactions, in which H 2 And the volume fraction of CO is 93%. and H 2 / CO is 1.8. Synthetic reducing gas moves upwards, heats and reduces the laterite nickel ore oxide pellets moving from top to bottom in the upper part of the hydrogen shaft furnace, and the reduction time is 3 hours. ...
PUM
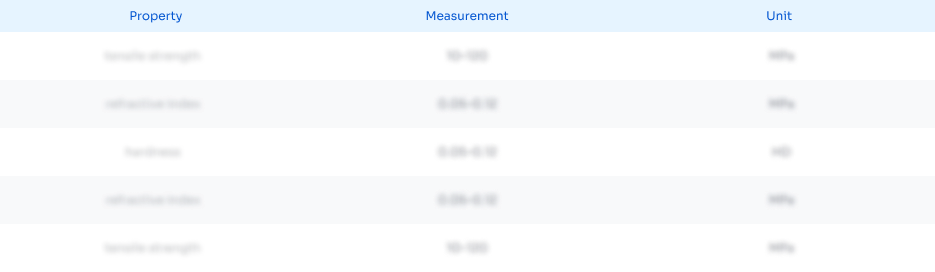
Abstract
Description
Claims
Application Information

- R&D Engineer
- R&D Manager
- IP Professional
- Industry Leading Data Capabilities
- Powerful AI technology
- Patent DNA Extraction
Browse by: Latest US Patents, China's latest patents, Technical Efficacy Thesaurus, Application Domain, Technology Topic, Popular Technical Reports.
© 2024 PatSnap. All rights reserved.Legal|Privacy policy|Modern Slavery Act Transparency Statement|Sitemap|About US| Contact US: help@patsnap.com