Environment-friendly rubber regenerating process
An environmentally friendly rubber and process technology, applied in the direction of plastic recycling, recycling technology, etc., can solve the problems of unfavorable industrial production, low output, high energy consumption, etc., achieve the effects of no environmental pollution, reduce production costs, and improve the quality of rubber materials
- Summary
- Abstract
- Description
- Claims
- Application Information
AI Technical Summary
Problems solved by technology
Method used
Examples
Embodiment 1
[0015] An environmentally friendly rubber regeneration process of the present invention includes the following steps: firstly select waste rubber that meets the specifications, perform cleaning, impurity removal, and sorting steps, and then use a crusher to crush, and the crushing is divided into coarse crushing, medium crushing, fine crushing, and fine crushing The final rubber fineness is 30 mesh, and the crushed rubber is placed in a reaction kettle, the temperature in the reaction kettle is 250°C, and the reaction time is 2.5h. Add desulfurizer, antioxidant and softener, desulfurizer, antioxidant and The ratio of softener input is 150:1:2. After fully reacting, the rubber is placed in a cooling tower for cooling. The temperature in the cooling tower is 100°C. The cooled rubber is pressed by the refining machine and open mill in the rubber pressing equipment. Sheets are made into recycled rubber products.
Embodiment 2
[0017] An environmentally friendly rubber regeneration process of the present invention includes the following steps: firstly select waste rubber that meets the specifications, perform cleaning, impurity removal, and sorting steps, and then use a crusher to crush, and the crushing is divided into coarse crushing, medium crushing, fine crushing, and fine crushing The fineness of the final rubber is 25 mesh, and the crushed rubber is placed in a reaction kettle. The temperature in the reaction kettle is 300 ° C, and the reaction time is 2.6 hours. Add desulfurizer, antioxidant and softener, desulfurizer, antioxidant and The ratio of softener input is 160:1:2. After fully reacting, the rubber is placed in a cooling tower for cooling. The temperature in the cooling tower is 110°C. The cooled rubber is pressed by the refining machine and open mill in the rubber pressing equipment. Sheets are made into recycled rubber products.
Embodiment 3
[0019] An environmentally friendly rubber regeneration process of the present invention includes the following steps: firstly select waste rubber that meets the specifications, perform cleaning, impurity removal, and sorting steps, and then use a crusher to crush, and the crushing is divided into coarse crushing, medium crushing, fine crushing, and fine crushing The final rubber fineness reaches 20 meshes, and the crushed rubber is placed in a reactor. The temperature in the reactor is 320°C, and the reaction time is 2.8 hours. Add desulfurizer, antioxidant and softener, desulfurizer, antioxidant and The ratio of softener input is 170:1:2. After fully reacting, the rubber is placed in a cooling tower for cooling. The temperature in the cooling tower is 120°C. The cooled rubber is pressed by the refining machine and open mill in the rubber pressing equipment. Sheets are made into recycled rubber products.
PUM
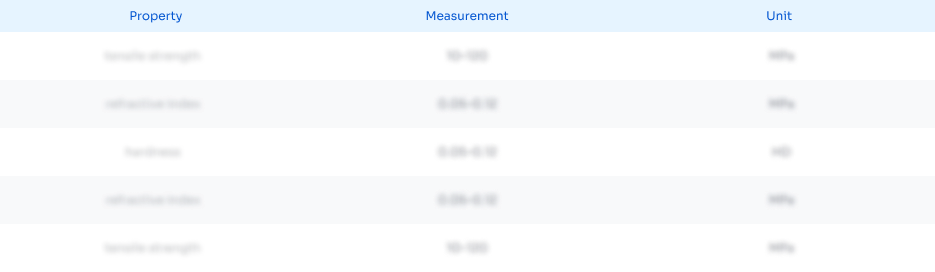
Abstract
Description
Claims
Application Information

- R&D
- Intellectual Property
- Life Sciences
- Materials
- Tech Scout
- Unparalleled Data Quality
- Higher Quality Content
- 60% Fewer Hallucinations
Browse by: Latest US Patents, China's latest patents, Technical Efficacy Thesaurus, Application Domain, Technology Topic, Popular Technical Reports.
© 2025 PatSnap. All rights reserved.Legal|Privacy policy|Modern Slavery Act Transparency Statement|Sitemap|About US| Contact US: help@patsnap.com