Anti-freezing cement
A technology of cement and Portland cement, which is applied in the field of antifreeze cement, can solve the problems of complex construction, insecure construction, and unsuitability for large-scale application, and achieve the effect of good antifreeze effect, good long-term durability, and reduced possibility of freezing damage
- Summary
- Abstract
- Description
- Claims
- Application Information
AI Technical Summary
Problems solved by technology
Method used
Examples
Embodiment 1
[0012] An antifreeze cement is composed of the following parts by weight: 15 parts of calcium chloride, 5 parts of sodium chloride, 1 part of sodium nitrite, 8 parts of sodium chloride, 15 parts of gypsum, 5 parts of alum, metaaluminic acid 10 parts of calcium, 15 parts of sodium thiocyanate, 25 parts of calcium silicate hydrate, 15 parts of triethanolamine, 15 parts of glass fiber, 25 parts of sodium carbonate, 60 parts of Portland cement clinker.
[0013] Further, an antifreeze cement is prepared by the following method: crushing and drying each raw material, batching, grinding, calcining, stirring, and grinding, adding other antifreeze components into the calcined clinker, and putting it into the stirred After being fully stirred in the device, they are co-ground to make cement products.
Embodiment 2
[0015] An antifreeze cement is composed of the following parts by weight: 20 parts of calcium chloride, 10 parts of sodium chloride, 5 parts of sodium nitrite, 12 parts of sodium chloride, 25 parts of gypsum, 10 parts of alum, metaaluminic acid 15 parts of calcium, 20 parts of sodium thiocyanate, 35 parts of calcium silicate hydrate, 22 parts of triethanolamine, 20 parts of glass fiber, 30 parts of sodium carbonate, 70 parts of Portland cement clinker.
[0016] Further, an antifreeze cement is prepared by the following method: crushing and drying each raw material, batching, grinding, calcining, stirring, and grinding, adding other antifreeze components into the calcined clinker, and putting it into the stirred After being fully stirred in the device, they are co-ground to make cement products.
Embodiment 3
[0018] An antifreeze cement is composed of the following parts by weight: 18 parts of calcium chloride, 8 parts of sodium chloride, 4 parts of sodium nitrite, 10 parts of sodium chloride, 20 parts of gypsum, 8 parts of alum, metaaluminic acid 12 parts of calcium, 18 parts of sodium thiocyanate, 30 parts of calcium silicate hydrate, 20 parts of triethanolamine, 18 parts of glass fiber, 28 parts of sodium carbonate, 65 parts of Portland cement clinker.
[0019] Further, an antifreeze cement is prepared by the following method: crushing and drying each raw material, batching, grinding, calcining, stirring, and grinding, adding other antifreeze components into the calcined clinker, and putting it into the stirred After being fully stirred in the device, they are co-ground to make cement products.
PUM
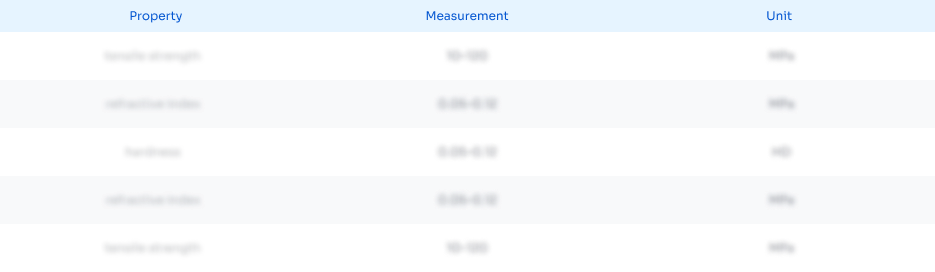
Abstract
Description
Claims
Application Information

- R&D Engineer
- R&D Manager
- IP Professional
- Industry Leading Data Capabilities
- Powerful AI technology
- Patent DNA Extraction
Browse by: Latest US Patents, China's latest patents, Technical Efficacy Thesaurus, Application Domain, Technology Topic, Popular Technical Reports.
© 2024 PatSnap. All rights reserved.Legal|Privacy policy|Modern Slavery Act Transparency Statement|Sitemap|About US| Contact US: help@patsnap.com