Thin film cutting device
A cutting and film technology, which is applied in the stacking receiving device, thin material handling, transportation and packaging, etc., can solve the problems of uneven film stacking, film burr production capacity, and unfavorable roll film cleaning, etc. It is convenient for subsequent process operations, high-quality cutting, and the effect of eliminating static electricity
- Summary
- Abstract
- Description
- Claims
- Application Information
AI Technical Summary
Problems solved by technology
Method used
Image
Examples
Embodiment Construction
[0027] The present application will be described in further detail below in conjunction with the accompanying drawings and specific embodiments. It should be understood that the following exemplary embodiments and descriptions are only used to explain the present invention, not as a limitation to the present invention, and, in the case of no conflict, the embodiments in the application and the features in the embodiments can be combined with each other .
[0028] In order to explain the positional relationship of the structure more clearly, unless otherwise specified, the "downstream side" and "upstream side" mentioned below refer to the upstream side where the film passes first according to the traveling direction of the film, and the position where the film passes behind The position is on the downstream side.
[0029] Such as Figure 1 to Figure 8 As shown, one embodiment of the present invention provides a film cutting device, comprising:
[0030] A feeding mechanism 1 ...
PUM
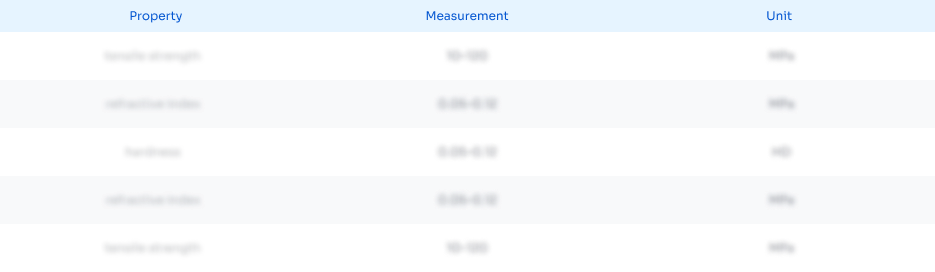
Abstract
Description
Claims
Application Information

- R&D Engineer
- R&D Manager
- IP Professional
- Industry Leading Data Capabilities
- Powerful AI technology
- Patent DNA Extraction
Browse by: Latest US Patents, China's latest patents, Technical Efficacy Thesaurus, Application Domain, Technology Topic, Popular Technical Reports.
© 2024 PatSnap. All rights reserved.Legal|Privacy policy|Modern Slavery Act Transparency Statement|Sitemap|About US| Contact US: help@patsnap.com