High speed railway safety detection system based on air-rail dual-purpose unmanned plane
A technology for safety detection and high-speed railways, applied in the field of unmanned aerial vehicles, can solve the problems of high cost, occupying normal driving space, poor flexibility, etc., and achieve the effect of low cost, high flexibility, and strong anti-interference ability
- Summary
- Abstract
- Description
- Claims
- Application Information
AI Technical Summary
Problems solved by technology
Method used
Image
Examples
Embodiment Construction
[0023] 1-body, 2-rotating blades, 3-casing, 4-high-definition camera, 5-propelling propeller, 6-horizontal guide wheel, 7-telescopic connecting rod, 8-ultrasonic rangefinder, 9-stepping motor, 10 - U-bar, 11-rolling wheels.
[0024] (1) UAV design
[0025] Classified by scale, UAVs can be divided into micro UAVs, light UAVs, small UAVs, and large UAVs. The present invention considers that the actual situation on the railway is not complicated, and its own workload is not large. Through comparative analysis, the four-rotor light UAV selected by the present invention, such as figure 1 shown. Based on the current experimental environment, some main parameters of the UAV in this scheme are listed in Table 1, such as flight height, flight time, wind resistance, etc. The UAV has a long load flight time and low vibration during flight, which is convenient for the measurement of the ultrasonic height sensor in the test, and can carry 2 kg, which can meet the experimental requiremen...
PUM
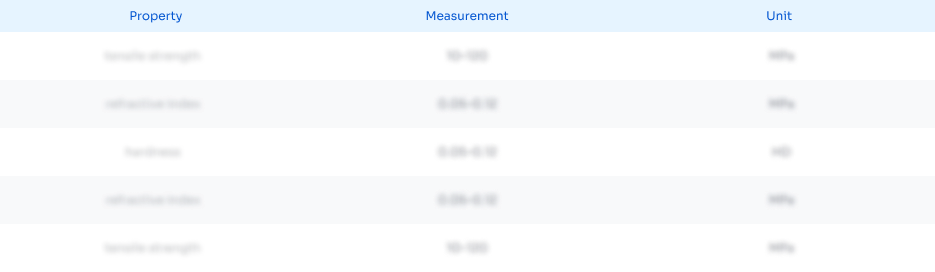
Abstract
Description
Claims
Application Information

- R&D
- Intellectual Property
- Life Sciences
- Materials
- Tech Scout
- Unparalleled Data Quality
- Higher Quality Content
- 60% Fewer Hallucinations
Browse by: Latest US Patents, China's latest patents, Technical Efficacy Thesaurus, Application Domain, Technology Topic, Popular Technical Reports.
© 2025 PatSnap. All rights reserved.Legal|Privacy policy|Modern Slavery Act Transparency Statement|Sitemap|About US| Contact US: help@patsnap.com