Flow-casting production equipment for zirconium oxide substrates
A zirconia-based, production equipment technology, applied in the field of zirconia substrate casting production equipment, can solve the problems of bending cracking, easy generation of surface stripes, and stripes on the surface of the green sheet, etc., to achieve outstanding substantive features, high efficiency and high quality Production, uniform thickness effect
- Summary
- Abstract
- Description
- Claims
- Application Information
AI Technical Summary
Problems solved by technology
Method used
Image
Examples
Embodiment Construction
[0017] As shown in the figure, the tape casting production equipment of zirconia substrate of the present invention comprises working platform 5, unwinding mechanism 1 and winding mechanism 8 that are located at the front and rear ends of working platform 5, and the surface of working platform 5 is paved with stainless steel plate material. Casting carrier plate, the film belt A unrolled by the unwinding mechanism 1 is rewound by the rewinding mechanism 8 after passing through the surface of the working platform 5 horizontally. 5. A casting device 2 is provided at one end close to the unwinding mechanism 1, and nine drying chambers 4 are arranged above the working platform 5 along the front and rear directions. The nine drying chambers communicate with each other and form a closed drying space above the working platform 5. In the enclosed drying space, a first exhaust pipe 3 is provided at the front end (inlet side of the first drying chamber), and a second exhaust pipe 6 is ar...
PUM
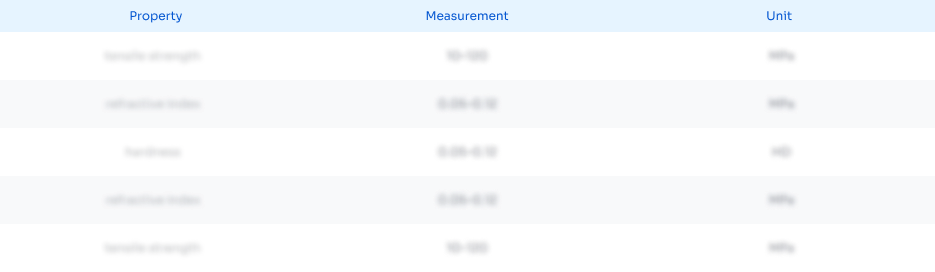
Abstract
Description
Claims
Application Information

- R&D
- Intellectual Property
- Life Sciences
- Materials
- Tech Scout
- Unparalleled Data Quality
- Higher Quality Content
- 60% Fewer Hallucinations
Browse by: Latest US Patents, China's latest patents, Technical Efficacy Thesaurus, Application Domain, Technology Topic, Popular Technical Reports.
© 2025 PatSnap. All rights reserved.Legal|Privacy policy|Modern Slavery Act Transparency Statement|Sitemap|About US| Contact US: help@patsnap.com