Multi-module dipping system
A module and paste technology, which is used in casting and forming equipment, metal processing equipment, manufacturing tools, etc., can solve the problems of module paste paste gas, incomplete module paste paste, etc., to save equipment costs and shorten coating time. The effect of coating time and speeding up coating efficiency
- Summary
- Abstract
- Description
- Claims
- Application Information
AI Technical Summary
Problems solved by technology
Method used
Image
Examples
Embodiment Construction
[0025] In order to make the technical means, creative features, objectives and functions achieved by the present invention clearer and easier to understand, the present invention will be further explained below in conjunction with the drawings and specific implementations:
[0026] Reference Figure 1-4 , The present invention proposes a multi-module dipping system, which includes a slurry tank 100, and also includes the following units:
[0027] The module loading unit 200 can be dropped into the slurry tank 100. The module loading unit 200 includes a multilayer grid 210 and a plurality of connecting rods 220 connecting the multilayer grid 210 together, The plurality of connecting rods 220 are distributed around the outside of the grid 210 and the upper part is connected to a top plate 230. At least a part of the connecting rods 220 are axially provided with a slurry scraper 240. The upper end of the slurry scraper 240 and the top plate The bottom side of 230 is fixed, and a plura...
PUM
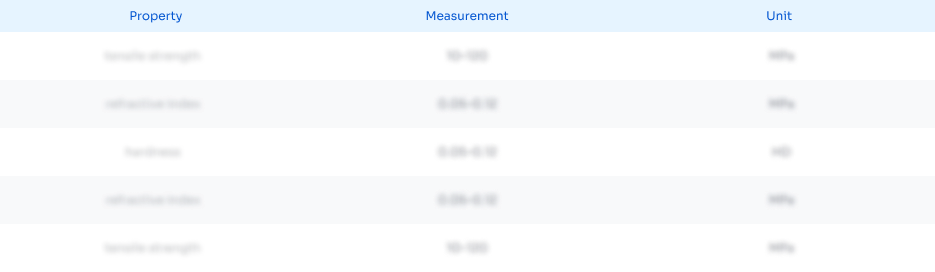
Abstract
Description
Claims
Application Information

- Generate Ideas
- Intellectual Property
- Life Sciences
- Materials
- Tech Scout
- Unparalleled Data Quality
- Higher Quality Content
- 60% Fewer Hallucinations
Browse by: Latest US Patents, China's latest patents, Technical Efficacy Thesaurus, Application Domain, Technology Topic, Popular Technical Reports.
© 2025 PatSnap. All rights reserved.Legal|Privacy policy|Modern Slavery Act Transparency Statement|Sitemap|About US| Contact US: help@patsnap.com