Engineering vehicle temperature control system and method based on double-cooling loop split radiator
A technology for engineering vehicles and temperature control systems. It is applied in the control of coolant flow, liquid cooling, and engine cooling. It can solve the uneven distribution of air volume on the surface of the radiator, the inability to meet the rapid temperature rise of the engine, and the uncontrollable speed of the cooling fan. problems, to avoid insufficient cooling capacity or excessive cooling problems, shorten the warm-up time, and reduce the effect of pressure drop
- Summary
- Abstract
- Description
- Claims
- Application Information
AI Technical Summary
Problems solved by technology
Method used
Image
Examples
Embodiment Construction
[0019] The detailed content of the present invention and its specific implementation will be further described below in conjunction with the accompanying drawings.
[0020] see figure 1As shown, the engineering vehicle temperature control system based on the dual cooling circuit split radiator of the present invention includes a high temperature cooling circuit, a low temperature cooling circuit, an engine 1, a heat collecting device 9, an intercooler 8, a high temperature radiator 5, a low temperature heat dissipation 15, auxiliary radiator 13, high temperature circuit water pump 6, low temperature circuit electric control water pump 10, electronic thermostat 3, fan 16, motor 11, first electromagnetic reversing valve 4, second electromagnetic reversing valve 14, ECU7, When the high-temperature circuit temperature sensor 2, the low-temperature circuit temperature sensor 12, and the electronic thermostat 3 are not turned on, the engine 1 coolant returns to the engine 1 through ...
PUM
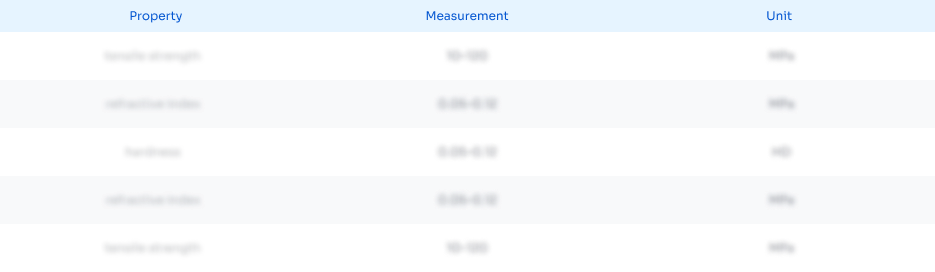
Abstract
Description
Claims
Application Information

- R&D
- Intellectual Property
- Life Sciences
- Materials
- Tech Scout
- Unparalleled Data Quality
- Higher Quality Content
- 60% Fewer Hallucinations
Browse by: Latest US Patents, China's latest patents, Technical Efficacy Thesaurus, Application Domain, Technology Topic, Popular Technical Reports.
© 2025 PatSnap. All rights reserved.Legal|Privacy policy|Modern Slavery Act Transparency Statement|Sitemap|About US| Contact US: help@patsnap.com