A stamping device for a punching machine
A stamping device and technology of a punching machine, which is applied in the field of stamping devices of a punching machine, can solve the problems of reduced precision of the punching machine, increased friction of the crankshaft mechanism, and wear, and achieve the effects of smooth operation of the crankshaft mechanism, reduced use requirements, and high service life
- Summary
- Abstract
- Description
- Claims
- Application Information
AI Technical Summary
Problems solved by technology
Method used
Image
Examples
Embodiment Construction
[0026] The following are specific embodiments of the present invention and in conjunction with the accompanying drawings, the technical solutions of the present invention are further described, but the present invention is not limited to these embodiments.
[0027] Such as figure 1 and figure 2 As shown, the present invention provides a stamping device for a punch press, including a mounting frame 100, the mounting plate 120 is provided on the mounting frame 100, and a first mounting position 160 is provided on the upper end surface of the mounting plate 120. The second installation position 170 and the third installation position 180 are provided on the lower end surface of the installation plate 120, and the second installation position 170 and the third installation position 180 are separated by a partition 410; the motor 110 is arranged on the first installation position 160 On the side, the motor 110 has a power shaft, and the power shaft is sleeved with a runner 111; t...
PUM
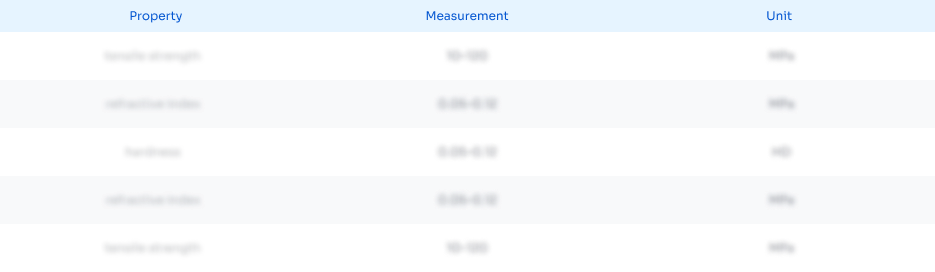
Abstract
Description
Claims
Application Information

- Generate Ideas
- Intellectual Property
- Life Sciences
- Materials
- Tech Scout
- Unparalleled Data Quality
- Higher Quality Content
- 60% Fewer Hallucinations
Browse by: Latest US Patents, China's latest patents, Technical Efficacy Thesaurus, Application Domain, Technology Topic, Popular Technical Reports.
© 2025 PatSnap. All rights reserved.Legal|Privacy policy|Modern Slavery Act Transparency Statement|Sitemap|About US| Contact US: help@patsnap.com