A kind of acid dye foam printing solution and foam printing method of nylon thin fabric
An acid dye and thin fabric technology, applied in the field of textile printing and dyeing, can solve the problems of large pulp content in printing paste, inability to print multiple sets of colors, and high fiber fineness density, and achieves good printing effect, superior economic benefits, and water retention. high effect
- Summary
- Abstract
- Description
- Claims
- Application Information
AI Technical Summary
Problems solved by technology
Method used
Image
Examples
Embodiment 1
[0021] The foam printing solution of the present embodiment comprises the following raw materials in parts by weight: Pula Red B 15g / L, sodium lauryl sulfate 1.5g / L, the composite stabilizer consumption is 0.5g / L, and the composite stabilizer is positive dodecyl Alcohol and sodium carboxymethylcellulose (CMC-Na), the mass ratio of n-dodecyl alcohol to CMC-Na is 1:0.1, the thickener is 4g / L, and the thickener is carboxymethylcellulose The compound of sodium and guar gum, the mass ratio of sodium carboxymethyl cellulose and guar gum is 1:0.1.
[0022] The method of utilizing the above-mentioned raw materials to carry out foam printing on nylon thin fabrics is:
[0023] (1) Stir and mix the above-mentioned acid dye components with a mixer in advance, then add them into the feeding cylinder of the foaming machine for foaming, and set the parameters of the foaming machine. The parameters of the foaming device: the feed rate is 0.30g / l, the rotor speed is 960 rpm, and the foaming r...
Embodiment 2
[0029] The foam printing solution of the present embodiment comprises the following raw materials by weight: weak acid yellow GN 30g / L, sodium lauryl sulfate 3g / L, composite stabilizer consumption is 2g / L, n-dodecyl alcohol and CMC in the composite stabilizer -The mass ratio of Na is 1:1, the thickener 6g / L, and the mass ratio of sodium carboxymethylcellulose and guar gum in the thickener is 1:0.3.
[0030] The method of utilizing the above-mentioned raw materials to carry out foam printing on nylon thin fabrics is:
[0031] (1) Stir and mix the above-mentioned acid dye components with a mixer in advance, then add them into the feeding cylinder of the foaming machine for foaming, and set the parameters of the foaming machine. The parameters of the foaming device: the feed rate is 0.30g / l, the rotor speed is 960 rpm, and the foaming ratio (BR) is 7;
[0032] (2) The foam is transported to the foam application device through the catheter, and then the foam is evenly distributed...
Embodiment 3
[0037] The foam printing liquid of the present embodiment comprises the raw material of following weight portion: weak acid brilliant blue Rawl 75g / L, sodium lauryl sulfate 3g / L, composite stabilizer consumption is 3g / L, the mass ratio of n-dodecyl alcohol and CMC The thickener is 1:1.5, the thickener is 7g / L, and the mass ratio of sodium carboxymethylcellulose and guar gum in the thickener is 1:0.5.
[0038] The method of utilizing the above-mentioned raw materials to carry out foam printing on nylon thin fabrics is:
[0039] (1) Stir and mix the above-mentioned acid dye components with a mixer in advance, then add them into the feeding cylinder of the foaming machine for foaming, and set the parameters of the foaming machine. The parameters of the foaming device: the feed rate is 0.30g / l, the rotor speed is 960 rpm, and the foaming ratio (BR) is 9;
[0040] (2) The foam is transported to the foam application device through the catheter, and then the foam is evenly distribut...
PUM
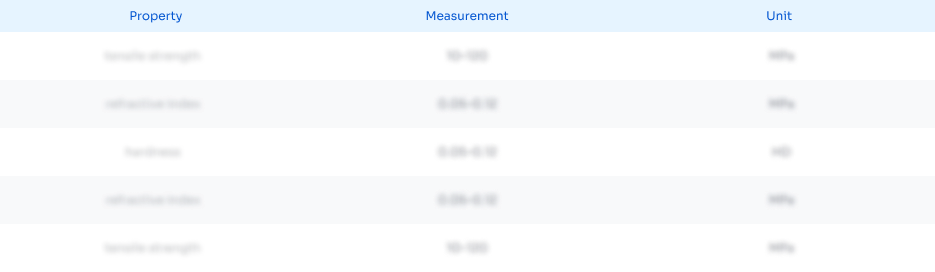
Abstract
Description
Claims
Application Information

- R&D Engineer
- R&D Manager
- IP Professional
- Industry Leading Data Capabilities
- Powerful AI technology
- Patent DNA Extraction
Browse by: Latest US Patents, China's latest patents, Technical Efficacy Thesaurus, Application Domain, Technology Topic, Popular Technical Reports.
© 2024 PatSnap. All rights reserved.Legal|Privacy policy|Modern Slavery Act Transparency Statement|Sitemap|About US| Contact US: help@patsnap.com