Milling type electrical discharge machining device for self-repairing tool electrode and method
A tool electrode and electric discharge machining technology, which is applied in the field of self-repairing tool electrode milling electric discharge machining devices, can solve problems that affect machining accuracy and quality, electrode damage, and prone to stray corrosion
- Summary
- Abstract
- Description
- Claims
- Application Information
AI Technical Summary
Problems solved by technology
Method used
Image
Examples
Embodiment Construction
[0029] The invention provides a self-repairing tool electrode milling type electrical discharge machining device and method, so as to achieve the purposes of prolonging the service life of the tool electrode, improving the machining accuracy, improving the machining quality, and reducing the machining cost.
[0030] The following will clearly and completely describe the technical solutions in the embodiments of the present invention with reference to the accompanying drawings in the embodiments of the present invention. Obviously, the described embodiments are only some, not all, embodiments of the present invention. Based on the embodiments of the present invention, all other embodiments obtained by persons of ordinary skill in the art without making creative efforts belong to the protection scope of the present invention.
[0031] see Figure 1-Figure 3 ., figure 1 It is a schematic structural diagram of a self-repairing tool electrode milling electric discharge machining d...
PUM
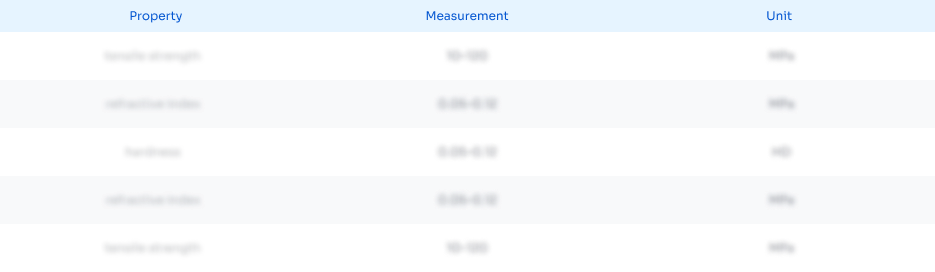
Abstract
Description
Claims
Application Information

- R&D Engineer
- R&D Manager
- IP Professional
- Industry Leading Data Capabilities
- Powerful AI technology
- Patent DNA Extraction
Browse by: Latest US Patents, China's latest patents, Technical Efficacy Thesaurus, Application Domain, Technology Topic, Popular Technical Reports.
© 2024 PatSnap. All rights reserved.Legal|Privacy policy|Modern Slavery Act Transparency Statement|Sitemap|About US| Contact US: help@patsnap.com