Preparation method of SBS asphalt stabilizer
A stabilizer and asphalt technology, applied in the field of asphalt additives, can solve the problems of easy segregation and performance degradation of modified asphalt, and achieve the effects of improving storage stability, improving performance and flexibility.
- Summary
- Abstract
- Description
- Claims
- Application Information
AI Technical Summary
Problems solved by technology
Method used
Examples
Embodiment 1
[0026] 1) Grind the calcium carbonate and sieve it to less than 0.1 μm to obtain calcium carbonate powder; add 100 g of calcium carbonate powder and 10 g of butyl titanate into 800 mL of absolute ethanol solvent to disperse evenly; heat in a water bath to 45 °C , reflux reaction for 60 minutes, centrifuged, and the resulting solid was dried in a vacuum oven to obtain active calcium carbonate;
[0027] 2) Weigh 25 parts of sulfur powder, 16 parts of SBS, 12 parts of styrene-butadiene rubber, 1.5 parts of stearylamine polyoxyethylene ether, 1.5 parts of stearyl trimethylammonium chloride, 7 parts of polyethylene resin, and nanometer zinc oxide Put 4 parts into the grinder, heat to 130°C, shear and grind to mix evenly, continue to add 45 parts of active calcium carbonate and 1.5 parts of polyoxyethylene nonylphenyl ether prepared in step 1), heat up to 185°C, shear and grind Mix evenly, extrude and granulate through a twin-screw extruder, and cut into pellets through a pelletizer...
Embodiment 2
[0029] 1) Grind the calcium carbonate and sieve it to less than 0.1 μm to obtain calcium carbonate powder; add 100 g of calcium carbonate powder and 10 g of butyl titanate into 500 mL of absolute ethanol solvent to disperse evenly; heat in a water bath to 40 °C , reflux reaction for 90min, centrifuged, and the obtained solid was dried in a vacuum oven to obtain active calcium carbonate;
[0030] 2) Weigh 35 parts of sulfur powder, 18 parts of SBS, 18 parts of styrene-butadiene rubber, 2.5 parts of stearylamine polyoxyethylene ether, 2.5 parts of stearyl trimethylammonium chloride, 9 parts of polyethylene resin, and nanometer zinc oxide Put 5 parts into the grinder, heat to 120°C, shear and grind to mix evenly, continue to add 55 parts of active calcium carbonate and 2.5 parts of polyoxyethylene nonylphenyl ether prepared in step 1), heat up to 180°C, shear and grind Mix evenly, extrude and granulate through a twin-screw extruder, and cut into pellets through a pelletizer to ob...
Embodiment 3
[0032] 1) Grind the calcium carbonate and sieve it to less than 0.1 μm to obtain calcium carbonate powder; add 100 g of calcium carbonate powder and 10 g of butyl titanate into 1000 mL of absolute ethanol solvent to disperse evenly; heat in a water bath to 50 °C , reflux reaction for 45min, centrifuged, and the resulting solid was dried in a vacuum oven to obtain active calcium carbonate;
[0033] 2) Weigh 30 parts of sulfur powder, 17 parts of SBS, 15 parts of styrene-butadiene rubber, 2 parts of stearylamine polyoxyethylene ether, 2 parts of stearyl trimethylammonium chloride, 8 parts of polyethylene resin, and nano-zinc oxide Put 4.5 parts into the grinder, heat to 150°C, shear and grind to mix evenly, continue to add 50 parts of active calcium carbonate and 2 parts of polyoxyethylene nonylphenyl ether prepared in step 1), heat up to 190°C, shear and grind Mix evenly, extrude and granulate through a twin-screw extruder, and cut into pellets through a pelletizer to obtain th...
PUM
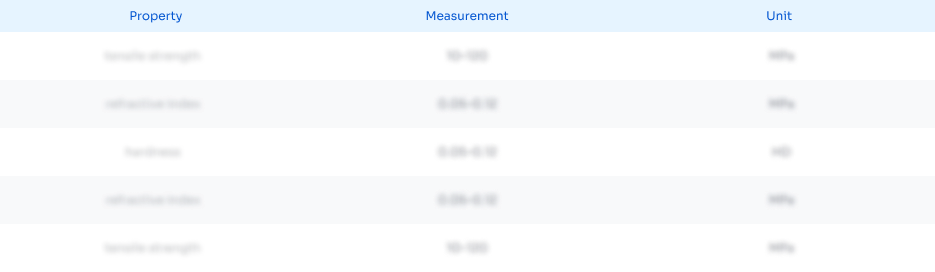
Abstract
Description
Claims
Application Information

- R&D
- Intellectual Property
- Life Sciences
- Materials
- Tech Scout
- Unparalleled Data Quality
- Higher Quality Content
- 60% Fewer Hallucinations
Browse by: Latest US Patents, China's latest patents, Technical Efficacy Thesaurus, Application Domain, Technology Topic, Popular Technical Reports.
© 2025 PatSnap. All rights reserved.Legal|Privacy policy|Modern Slavery Act Transparency Statement|Sitemap|About US| Contact US: help@patsnap.com