Cooling structure of busbar mold
A cooling structure and busbar technology, applied in the field of cooling structures, can solve the problems of different cooling effects, large cooling effects, and large fluctuations in temperature difference, and achieve the effects of high cooling efficiency, elimination of influence, and reduction of contact
- Summary
- Abstract
- Description
- Claims
- Application Information
AI Technical Summary
Problems solved by technology
Method used
Image
Examples
Embodiment 1
[0025] Embodiment one, such as Figure 1 to Figure 3 As shown, the embodiment of the present invention includes a mold body 1, a plurality of linearly arranged molding grooves 2 are arranged on the mold body 1, and a cooling device 3 is arranged below the molding groove 2, and it is characterized in that: the mold body 1 includes a Groove 2 is a constant temperature area 1-1 for lead supply, a casting welding area 1-2 for casting welding, and a heat preservation area for insulating the casting welding area 1-2. The forming tank 2 is arranged in the casting welding area 1-2, The constant temperature zone 1-1, the casting and welding zone 1-2 and the heat preservation zone are independently equipped with heaters, and the heater mainly adopts a ceramic heating body. Each casting and welding zone 1-2 is correspondingly equipped with an independent cooling device 3, and the cooling device 3 includes the cooling body 3-1 arranged under the casting and welding zone 1-2 and / or the hea...
PUM
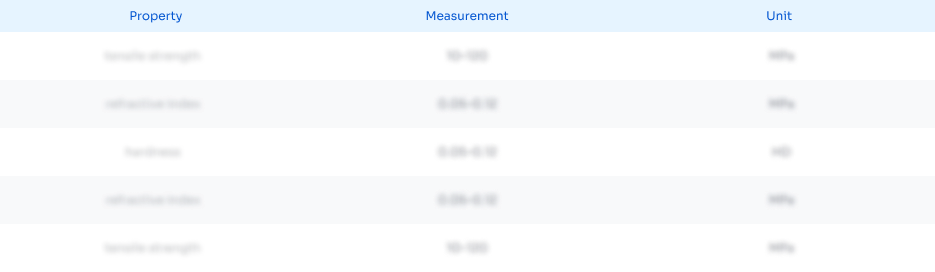
Abstract
Description
Claims
Application Information

- R&D Engineer
- R&D Manager
- IP Professional
- Industry Leading Data Capabilities
- Powerful AI technology
- Patent DNA Extraction
Browse by: Latest US Patents, China's latest patents, Technical Efficacy Thesaurus, Application Domain, Technology Topic, Popular Technical Reports.
© 2024 PatSnap. All rights reserved.Legal|Privacy policy|Modern Slavery Act Transparency Statement|Sitemap|About US| Contact US: help@patsnap.com