Preparation method of CPVC resin by water-phase suspension method
A technology of CPVC resin and PVC resin, which is applied in the field of preparation of CPVC resin by aqueous phase suspension method, can solve the problems of weakening the absorption capacity of CPVC resin additives, poor plasticization uniformity of CPVC resin, and hindering resin uniformity, etc., to achieve dynamic thermal stability Long time, good initial colorability, and the effect of reducing structural defects
- Summary
- Abstract
- Description
- Claims
- Application Information
AI Technical Summary
Problems solved by technology
Method used
Examples
Embodiment 1
[0025] Add 80kg of deionized water and 10kg of chlorinated PVC resin QS-C60 with a degree of polymerization of 800 into a 100L chlorination reactor, start the stirring and ultrasonic device, the ultrasonic frequency is 25MHz, after the PVC resin is suspended in the water phase, turn off the ultrasonic device. Add 150g of peroxydicarbonate with a concentration of 40%. After using chlorine gas to discharge the air in the kettle, raise the temperature of the reactor, slowly introduce chlorine gas, and turn on the ultrasonic device at the same time. When the temperature of the reactor reaches about 85°C, the chlorination reaction accelerates. The temperature of the reactor is 100°C, the speed of chlorine flow is controlled at 50g / min, and the pressure of the reactor is kept at 0.3MPa. After chlorination reaction for 20 minutes, the ultrasonic device is turned off. When the amount of chlorine flow reaches 6.8kg, the flow of chlorine is stopped, and a terminator with a concentration o...
Embodiment 2
[0027] Add 80kg of deionized water and 15kg of chlorinated PVC resin QS-C65 with a degree of polymerization of 850 into a 150L chlorination reactor, start the stirring and ultrasonic device, the ultrasonic frequency is 25MHz, after the PVC resin is suspended in the water phase, turn off the ultrasonic device . Add 200g of peroxydicarbonate with a concentration of 40%. After using chlorine gas to discharge the air in the kettle, raise the temperature of the reactor, slowly introduce chlorine gas, and turn on the ultrasonic device at the same time. When the temperature of the reactor reaches about 85°C, the chlorination reaction accelerates. The temperature of the reaction kettle is 95°C, the speed of chlorine flow is controlled at 60g / min, and the pressure of the reaction kettle is maintained at 0.3MPa. After chlorination reaction for 15 minutes, the ultrasonic device is turned off. When the amount of chlorine flow reaches 10kg, the flow of chlorine is stopped, and the concentra...
Embodiment 3
[0029] Add 80kg of deionized water and 18kg of chlorinated PVC resin QS-C65 with a degree of polymerization of 900 into a 100L chlorination reactor, start the stirring and ultrasonic device, the ultrasonic frequency is 25MHz, after the PVC resin is suspended in the water phase, turn off the ultrasonic device . Add a total of 100g of peroxydicarbonate and dibenzoyl peroxide with a concentration of 40%. After using chlorine gas to discharge the air in the reactor, raise the temperature of the reactor, slowly introduce chlorine gas, and turn on the ultrasonic device at the same time. The temperature of the reactor reaches about 85°C When the chlorination reaction is accelerated, the temperature of the reactor is controlled at 105°C, the rate of chlorine flow is controlled at 7.2g / min, and the pressure of the reactor is maintained at 0.3MPa. After 20 minutes of chlorination, the ultrasonic device is turned off, and when the amount of chlorine flow reaches 12.5kg, stop Pass chlorin...
PUM
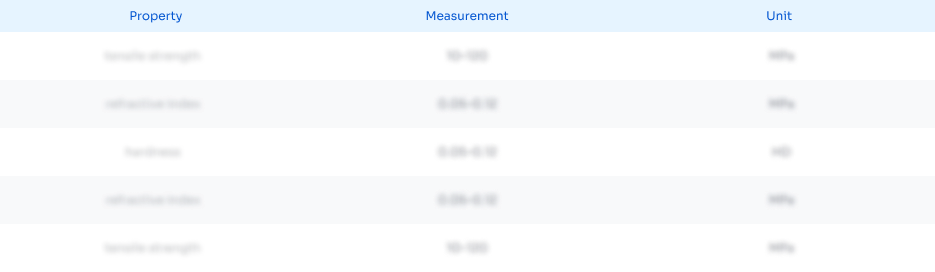
Abstract
Description
Claims
Application Information

- Generate Ideas
- Intellectual Property
- Life Sciences
- Materials
- Tech Scout
- Unparalleled Data Quality
- Higher Quality Content
- 60% Fewer Hallucinations
Browse by: Latest US Patents, China's latest patents, Technical Efficacy Thesaurus, Application Domain, Technology Topic, Popular Technical Reports.
© 2025 PatSnap. All rights reserved.Legal|Privacy policy|Modern Slavery Act Transparency Statement|Sitemap|About US| Contact US: help@patsnap.com