A 3D printing slicing method based on t-spline surface
A spline surface and 3D printing technology, which is applied in the fields of instruments, design optimization/simulation, calculation, etc., can solve problems such as difficult slicing and poor promotion
- Summary
- Abstract
- Description
- Claims
- Application Information
AI Technical Summary
Problems solved by technology
Method used
Image
Examples
Embodiment 1
[0132] Select a T-spline model with a free-form surface, such as Image 6 shown. The special feature of the surface is that it has a complex free-form surface appearance, but due to the advantages of the T-spline modeling theory, the complex model surface is expressed with only a few control vertices. The T-spline model is expressed by TSM file, the file size is 29KB; the model is expressed by STL file, the file size is 5072KB. The slice layer thickness is set to 0.1mm, and the data allowable error is 0.001mm.
[0133] Figure 7 The slicing results and local amplification effects of the T-spline surface of Example 1 are shown, and it can be clearly seen that the T-spline surface realizes layered slicing according to the set layer thickness, which illustrates the effectiveness and accuracy of the method of the present invention. sex.
Embodiment 2
[0135] The selected T-spline surface to be sliced is as Figure 8 shown. The special feature of this curved surface is that there are multiple slicing contour rings at the same height, and it is necessary to use the multi-region contour slicing method in step 105 to realize slicing. The T-spline model is expressed by TSM file, the file size is 3KB; the model is expressed by STL, the file size is 2816KB. In order to clearly show the slice effect, this example chooses 1.0mm slice layer thickness, and the data allowable error is 0.001mm.
[0136] Figure 9 shows the effect of multi-region T-spline surface slicing, Figure 10 is the left view of the slice profile, Figure 11 A top view of the slice profile. It can be clearly seen that the multi-region slicing method for T-spline curved surfaces proposed by the present invention can effectively realize the recognition and slicing functions of multi-contours of T-spline curved surfaces at the same height, which illustrates th...
PUM
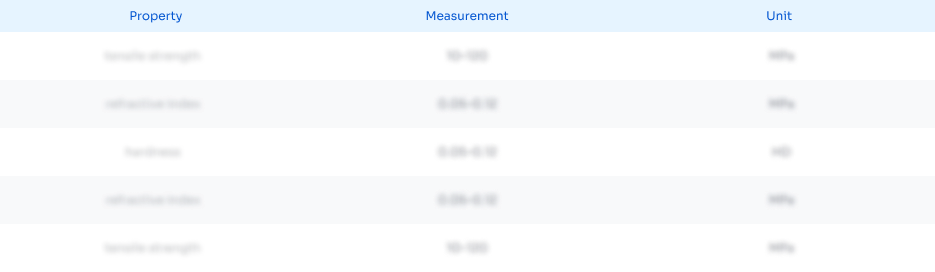
Abstract
Description
Claims
Application Information

- Generate Ideas
- Intellectual Property
- Life Sciences
- Materials
- Tech Scout
- Unparalleled Data Quality
- Higher Quality Content
- 60% Fewer Hallucinations
Browse by: Latest US Patents, China's latest patents, Technical Efficacy Thesaurus, Application Domain, Technology Topic, Popular Technical Reports.
© 2025 PatSnap. All rights reserved.Legal|Privacy policy|Modern Slavery Act Transparency Statement|Sitemap|About US| Contact US: help@patsnap.com