Composite fault diagnosis method for hydraulic AGC system
A technology of composite faults and diagnostic methods, applied in the direction of machine/structural component testing, measuring devices, instruments, etc., can solve problems such as piled steel, potential safety hazards of equipment, difficult fault isolation and positioning, etc., and achieve the effect of improving the separation rate
- Summary
- Abstract
- Description
- Claims
- Application Information
AI Technical Summary
Problems solved by technology
Method used
Image
Examples
Embodiment Construction
[0039] In order to facilitate the understanding of those skilled in the art, the present invention will be further described below in conjunction with specific embodiments and accompanying drawings, and the contents mentioned in the implementation modes are not intended to limit the present invention.
[0040] Such as figure 1 As shown, a composite fault diagnosis method of a hydraulic AGC system of the present invention first builds a simulation model of the system according to the schematic diagram of rolling mill components, and then builds a multi-signal model of the system on this basis to obtain a fault dependency matrix, including the following steps :
[0041] Step 1. Dynamic modeling of rolling mill components: Equivalent the various links of the hydraulic AGC system to obtain its mathematical model, and dynamically model the rolling mill components, as follows;
[0042] 11) If figure 2 The principle of the hydraulic system shown is equivalent to the hydraulic cyli...
PUM
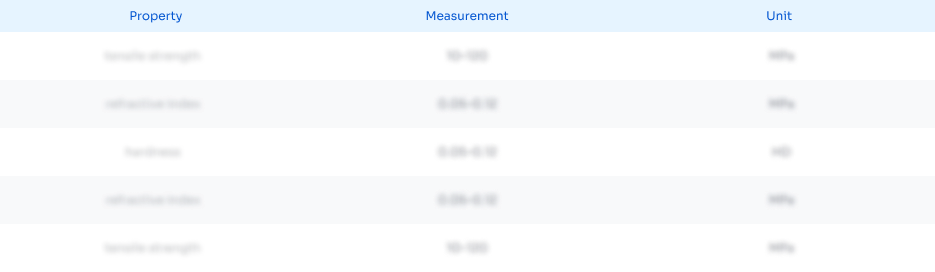
Abstract
Description
Claims
Application Information

- R&D
- Intellectual Property
- Life Sciences
- Materials
- Tech Scout
- Unparalleled Data Quality
- Higher Quality Content
- 60% Fewer Hallucinations
Browse by: Latest US Patents, China's latest patents, Technical Efficacy Thesaurus, Application Domain, Technology Topic, Popular Technical Reports.
© 2025 PatSnap. All rights reserved.Legal|Privacy policy|Modern Slavery Act Transparency Statement|Sitemap|About US| Contact US: help@patsnap.com