Hypersonic flight vehicle cooling and semiconductor thermoelectric power generation integrated system
A technology of thermoelectric power generation and hypersonic speed, applied in the direction of generators/motors, electrical components, etc., can solve problems such as insufficient fuel heat sinks, achieve the effects of reducing fuel consumption and maximum temperature, high reliability, and reducing quality penalties
- Summary
- Abstract
- Description
- Claims
- Application Information
AI Technical Summary
Problems solved by technology
Method used
Image
Examples
Embodiment approach 1
[0023] Implementation mode one: the following combination figure 1 The present embodiment will be described in detail. The hypersonic aircraft cooling and semiconductor thermoelectric power generation integrated system described in this embodiment includes a low-temperature channel 1, a semiconductor thermoelectric power generation device, multiple heat-conducting insulating layers 4 and a high-temperature channel 6;
[0024] The semiconductor thermoelectric power generation device block includes a plurality of N-type semiconductor thermoelectric materials 2, a plurality of P-type semiconductor thermoelectric materials 3 and a plurality of guide fins 5, the N-type semiconductor thermoelectric materials 2 and the P-type semiconductor thermoelectric materials 3 are arranged at intervals, And through the deflector 5 in series;
[0025] Both sides of the semiconductor thermoelectric power generation device are provided with a thermally conductive insulating layer 4 closely attach...
Embodiment approach 2
[0028] Implementation mode two: the following combination figure 2 The present embodiment will be described in detail. This embodiment is a further limitation of the hypersonic aircraft cooling and semiconductor thermoelectric power generation integrated system described in Embodiment 1. In this embodiment, the entrance of the low-temperature passage 1 and the entrance of the high-temperature passage 6 are located at the semiconductor thermoelectric power generation device. same side.
[0029] The opposite flow direction of the fuel in the low-temperature channel 1 and the high-temperature channel 6 causes uneven temperature difference, which is not conducive to improving the thermoelectric conversion efficiency, so the system structure is further improved, such as figure 2 shown. Both the inlet of the low-temperature channel 1 and the inlet of the high-temperature channel 6 are located on the left side of the semiconductor thermoelectric power generation device,
[0030]...
PUM
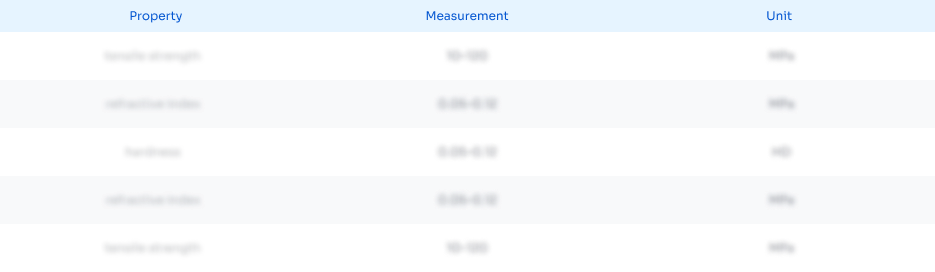
Abstract
Description
Claims
Application Information

- R&D
- Intellectual Property
- Life Sciences
- Materials
- Tech Scout
- Unparalleled Data Quality
- Higher Quality Content
- 60% Fewer Hallucinations
Browse by: Latest US Patents, China's latest patents, Technical Efficacy Thesaurus, Application Domain, Technology Topic, Popular Technical Reports.
© 2025 PatSnap. All rights reserved.Legal|Privacy policy|Modern Slavery Act Transparency Statement|Sitemap|About US| Contact US: help@patsnap.com