An automatic centering electric rotary chuck
An electric rotation and automatic centering technology, which is applied in auxiliary welding equipment, welding equipment, manufacturing tools, etc., can solve the problems of coil spring fatigue, difficult to guarantee machining accuracy, and large coil spring force
- Summary
- Abstract
- Description
- Claims
- Application Information
AI Technical Summary
Problems solved by technology
Method used
Image
Examples
Embodiment Construction
[0025] Below in conjunction with accompanying drawing and embodiment the present invention will be further described:
[0026] like Figure 1-3 As shown, an automatic centering electric rotary chuck includes a base 1, a bearing seat 2 is arranged on the base 1, a bearing 3 is arranged in the bearing seat 2, the inner ring of the bearing 3 is connected with the roller core 4, and one end of the roller core 4 is connected There is a roller core driving device, and the other end wall of the roller core is provided with two groups of gripper mechanisms 6 arranged in a cross shape, and the two gripper mechanisms 6 arranged symmetrically up and down are the first group of gripper mechanisms 7, and the symmetrically arranged left and right The two jaw mechanisms 6 are the second group of jaw mechanisms 8, at least one jaw mechanism 6 in each group of jaw mechanisms is provided with a sensor 32, the center of the roller core 4 is provided with a through hole 9, and the wall of the rol...
PUM
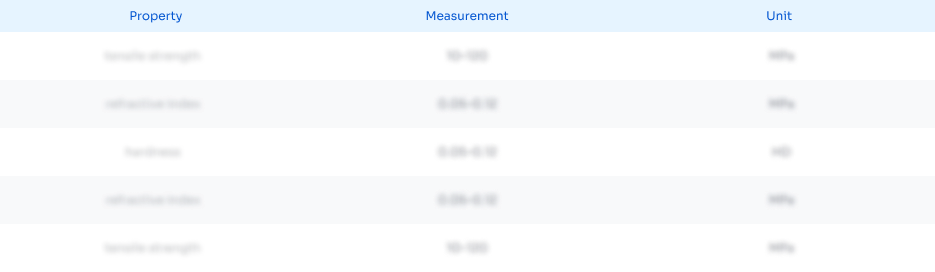
Abstract
Description
Claims
Application Information

- Generate Ideas
- Intellectual Property
- Life Sciences
- Materials
- Tech Scout
- Unparalleled Data Quality
- Higher Quality Content
- 60% Fewer Hallucinations
Browse by: Latest US Patents, China's latest patents, Technical Efficacy Thesaurus, Application Domain, Technology Topic, Popular Technical Reports.
© 2025 PatSnap. All rights reserved.Legal|Privacy policy|Modern Slavery Act Transparency Statement|Sitemap|About US| Contact US: help@patsnap.com