Preparation method of methyl-terminated propenol polyether
A technology of terminal allyl alcohol polyether and allyl alcohol polyoxyethylene ether, which is applied in the field of preparation of methyl-capped allyl alcohol polyether, can solve the problem of low capping rate, reduce the probability of occurrence, and reduce the concentration distribution Uniformity improvement, the effect of ensuring uniformity
- Summary
- Abstract
- Description
- Claims
- Application Information
AI Technical Summary
Problems solved by technology
Method used
Image
Examples
Embodiment 1
[0033](1) In the external circulation spray reactor (the average diameter of the droplet Sauter is 10 μm), add allyl alcohol polyoxyethylene ether raw material (molecular weight: 150) 150kg, remove oxygen and nitrogen replacement protection, open the external circulation pump for high-speed Cycle the spray.
[0034] (2) Controlling reaction temperature is 0 ℃, and liquid caustic soda (10%NaOH solution) 404kg raw material is sprayed in the reactor, feeds 51kg of monochloromethane raw material slowly simultaneously, realizes the sufficient mixing reaction of the three, and the feeding spraying time is 36 hours. After the feeding was finished, the heat preservation cycle spray reaction was continued for 12 hours, and the reaction ended.
[0035] (3) After the reaction is finished, the crude product is neutralized with 50% phosphoric acid, and then undergoes a post-treatment process of vacuum distillation and filtration to prepare a methyl-terminated allyl alcohol polyether produ...
Embodiment 2
[0037] (1) In the external circulation spray reactor (the average diameter of the droplet Sauter is 300 μm), add allyl alcohol polyoxyethylene ether raw material (molecular weight: 6000) 600kg, remove oxygen and nitrogen replacement protection, open the external circulation pump for high-speed Cycle the spray.
[0038] (2) Control the temperature at 60°C, spray 22.5 kg of potassium hydroxide solution (50% KOH) into the reactor, and slowly add 10.1 kg of monochloromethane raw material at the same time to realize the full mixing reaction of the three. for 2 hours. After the feeding was finished, the heat preservation cycle spray reaction was continued for 2 hours, and the reaction ended.
[0039] (3) After the reaction is finished, the crude product is neutralized with 50% phosphoric acid, and then undergoes a post-treatment process of vacuum distillation and filtration to prepare a methyl-terminated allyl alcohol polyether product. The color of the methyl-capped allyl alcohol...
Embodiment 3
[0041] (1) In the external circulation spray reactor (the average diameter of the droplet Sauter is 50 μm), add allyl alcohol polyoxyethylene ether raw material (molecular weight is 525) 525kg, remove oxygen and nitrogen replacement protection, open the external circulation pump for high-speed Cycle the spray.
[0042] (2) Control the temperature at 10°C, spray 243 kg of potassium hydroxide solution (30% KOH solution) into the reactor, and slowly add 65.6 kg of monochloromethane raw material to realize the full mixing reaction of the three. for 24 hours. After the feeding was finished, the heat preservation cycle spray reaction was continued for 6 hours, and the reaction ended.
[0043] (3) After the reaction is finished, the crude product is neutralized with 50% phosphoric acid, and then undergoes a post-treatment process of vacuum distillation and filtration to prepare a methyl-terminated allyl alcohol polyether product. The color of the methyl-capped allyl alcohol polyeth...
PUM
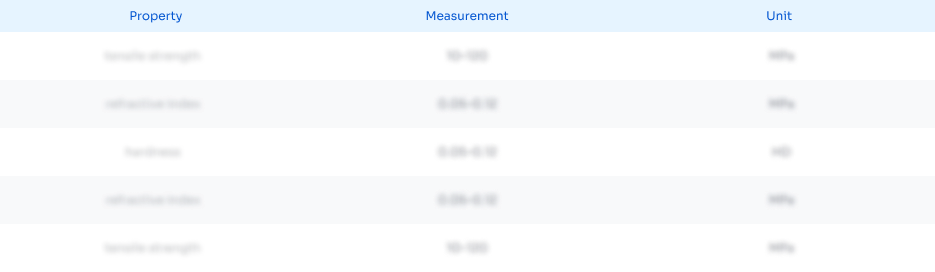
Abstract
Description
Claims
Application Information

- R&D
- Intellectual Property
- Life Sciences
- Materials
- Tech Scout
- Unparalleled Data Quality
- Higher Quality Content
- 60% Fewer Hallucinations
Browse by: Latest US Patents, China's latest patents, Technical Efficacy Thesaurus, Application Domain, Technology Topic, Popular Technical Reports.
© 2025 PatSnap. All rights reserved.Legal|Privacy policy|Modern Slavery Act Transparency Statement|Sitemap|About US| Contact US: help@patsnap.com