High-strength electric resistance welding casing pipe and manufacturing method thereof
A technology of resistance welding and high strength, which is applied in the field of straight seam resistance welding casing and its manufacturing, can solve the problems of high alloy cost, high strength, and difficulty in pipe making, and achieve low alloy cost, low performance, and consistency Effect
- Summary
- Abstract
- Description
- Claims
- Application Information
AI Technical Summary
Problems solved by technology
Method used
Image
Examples
Embodiment Construction
[0034] Below by embodiment the present invention will be further described.
[0035] In the embodiment of the present invention, according to the component ratio of the technical solution, smelting continuous casting, continuous casting slab reheating, rolling, cooling, coiling, ERW pipe making and whole pipe heat treatment are carried out. The composition of the steel of the embodiment of the present invention is shown in Table 1. The heating, rolling process and mechanical properties of the steel in the embodiment of the present invention are shown in Table 2. See Table 3 for the hot-rolled microstructure of the steel of the embodiment of the present invention. The steel of the embodiment of the present invention
[0036] The heat treatment process is shown in Table 4. The mechanical properties of the quenched and tempered state steel of the embodiment of the present invention are shown in Table 5.
[0037] Table 1 Composition of the steel of the embodiment of the presen...
PUM
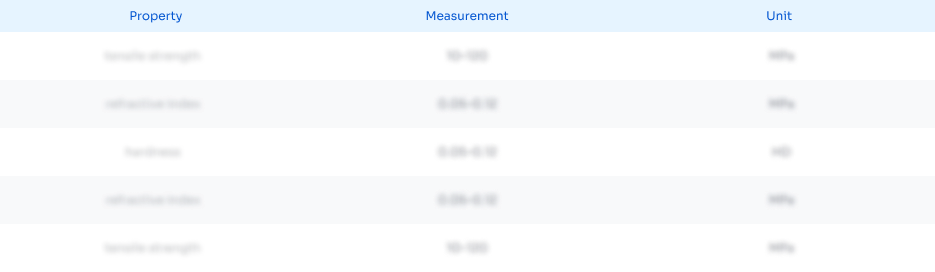
Abstract
Description
Claims
Application Information

- Generate Ideas
- Intellectual Property
- Life Sciences
- Materials
- Tech Scout
- Unparalleled Data Quality
- Higher Quality Content
- 60% Fewer Hallucinations
Browse by: Latest US Patents, China's latest patents, Technical Efficacy Thesaurus, Application Domain, Technology Topic, Popular Technical Reports.
© 2025 PatSnap. All rights reserved.Legal|Privacy policy|Modern Slavery Act Transparency Statement|Sitemap|About US| Contact US: help@patsnap.com