Gradient tungsten-copper composite and preparation method thereof
A composite material, tungsten-copper technology, applied in the field of gradient tungsten-copper composite material and its preparation, can solve problems such as no application, avoid forming cracks, ensure strength and precision, and improve conductivity.
- Summary
- Abstract
- Description
- Claims
- Application Information
AI Technical Summary
Problems solved by technology
Method used
Image
Examples
Embodiment 1
[0032] Such as figure 1 As shown, the gradient tungsten-copper composite material in this embodiment includes a tungsten skeleton 1 made by electron beam selective melting molding method and a copper filling phase 2 made by infiltration method. The tungsten skeleton 1 is arranged in multiple layers along its height direction. Each layer of tungsten skeleton 1 has a network porous structure, and the copper filling phase 2 is filled in the pores of each layer of tungsten skeleton 1, and the volume percentage of copper filling phase 2 increases or decreases layer by layer.
[0033] Such as figure 1 As shown, in the gradient tungsten-copper composite material of this embodiment, the tungsten skeleton 1 is represented by a grid-shaped black solid line, and the copper-filled phase 2 is represented by a gray filling color.
[0034] In this embodiment, the number of layers of the tungsten skeleton 1 is four layers, and the four-layer tungsten skeleton 1 is neatly stacked in the heigh...
Embodiment 2
[0048] Such as figure 1 As shown, the gradient tungsten-copper composite material in this embodiment includes a tungsten skeleton 1 made by electron beam selective melting molding method and a copper filling phase 2 made by infiltration method. The tungsten skeleton 1 is arranged in multiple layers along its height direction. Each layer of tungsten skeleton 1 has a network porous structure, and the copper filling phase 2 is filled in the pores of each layer of tungsten skeleton 1, and the volume percentage of copper filling phase 2 increases or decreases layer by layer.
[0049] Such as figure 1 As shown, in the gradient tungsten-copper composite material of this embodiment, the tungsten skeleton 1 is represented by a grid-shaped black solid line, and the copper-filled phase 2 is represented by a gray filling color.
[0050] In this embodiment, the number of layers of the tungsten skeleton 1 is four layers, and the four-layer tungsten skeleton 1 is neatly stacked in the heigh...
Embodiment 3
[0064] Such as figure 1 As shown, the gradient tungsten-copper composite material in this embodiment includes a tungsten skeleton 1 made by electron beam selective melting molding method and a copper filling phase 2 made by infiltration method. The tungsten skeleton 1 is arranged in multiple layers along its height direction. Each layer of tungsten skeleton 1 has a network porous structure, and the copper filling phase 2 is filled in the pores of each layer of tungsten skeleton 1, and the volume percentage of copper filling phase 2 increases or decreases layer by layer.
[0065] Such as figure 1 As shown, in the gradient tungsten-copper composite material of this embodiment, the tungsten skeleton 1 is represented by a grid-shaped black solid line, and the copper-filled phase 2 is represented by a gray filling color.
[0066] In this embodiment, the number of layers of the tungsten skeleton 1 is four layers, and the four-layer tungsten skeleton 1 is neatly stacked in the heigh...
PUM
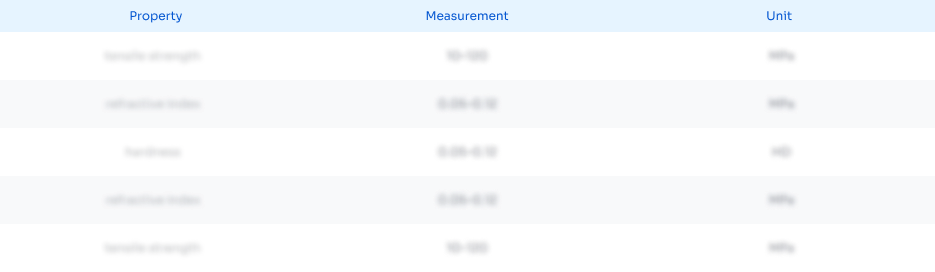
Abstract
Description
Claims
Application Information

- R&D
- Intellectual Property
- Life Sciences
- Materials
- Tech Scout
- Unparalleled Data Quality
- Higher Quality Content
- 60% Fewer Hallucinations
Browse by: Latest US Patents, China's latest patents, Technical Efficacy Thesaurus, Application Domain, Technology Topic, Popular Technical Reports.
© 2025 PatSnap. All rights reserved.Legal|Privacy policy|Modern Slavery Act Transparency Statement|Sitemap|About US| Contact US: help@patsnap.com