Socket
A socket and plug technology, applied in the assembly/disassembly of base/housing, contact parts, contact parts, etc., can solve the problems of sealing, component cost increase, restriction and so on
- Summary
- Abstract
- Description
- Claims
- Application Information
AI Technical Summary
Problems solved by technology
Method used
Image
Examples
Embodiment Construction
[0071] Below, use Figure 1 to Figure 8The socket 1 and its assembly method according to the first embodiment of the present invention will be described. It should be noted that, in this specification, the front side ( figure 1 The lower left side of the plug) is defined as the front, the back side along the insertion direction of the plug is defined as the rear, the bottom side facing the printed circuit board 50 is defined as the downward side, the upper side is defined as the upper side, and the direction of both sides is defined as Each part of the socket 1 will be described in the left-right direction.
[0072] The socket 1 of the present embodiment is formed by injection molding of synthetic resin of insulating material and formed into a "U"-shaped inner shell 2; by injection molding of synthetic resin of insulating material and formed into a cylindrical outer shell 3; The first blade terminal 5, the second blade terminal 6, the first ring terminal 7, the second ring ...
PUM
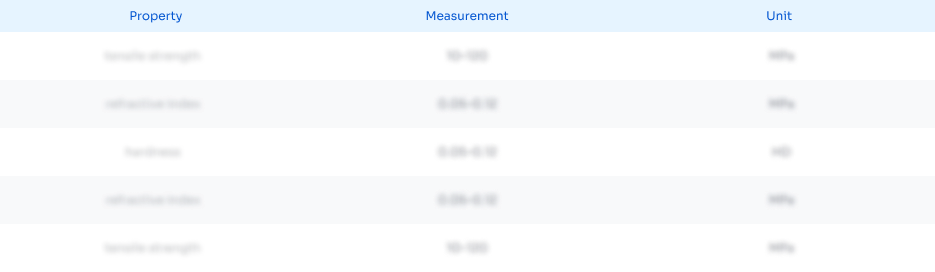
Abstract
Description
Claims
Application Information

- R&D Engineer
- R&D Manager
- IP Professional
- Industry Leading Data Capabilities
- Powerful AI technology
- Patent DNA Extraction
Browse by: Latest US Patents, China's latest patents, Technical Efficacy Thesaurus, Application Domain, Technology Topic, Popular Technical Reports.
© 2024 PatSnap. All rights reserved.Legal|Privacy policy|Modern Slavery Act Transparency Statement|Sitemap|About US| Contact US: help@patsnap.com