CMS/MnO2/PPY (carbon microsphere/manganese dioxide/polypyrrole) composite electrode material, as well as preparation method and application thereof
A composite electrode and mixed solution technology is applied in the field of composite materials to achieve the effects of easy commercialization and large-scale production, uniform PPY dispersion and low cost
- Summary
- Abstract
- Description
- Claims
- Application Information
AI Technical Summary
Problems solved by technology
Method used
Image
Examples
Embodiment 1
[0046] (A)CMS / MnO 2 Preparation of / PPY composite electrode material
[0047] Put 4g of glucose and 40mL of distilled water into a 50mL stainless steel reactor with built-in polytetrafluoroethylene, react at 180°C for 12h, then cool, centrifuge, wash thoroughly, and then dry at 60°C for 6h to obtain the carbon microsphere material; Add 0.05g of the carbon microsphere material prepared above, add 10mL of distilled water, and sonicate for 10min; weigh 0.25g of potassium permanganate, add it to the above mixed solution, stir to make it fully dissolve; then place it in an ultrasonic cleaning machine with an ultrasonic power of 400W Sonicate in the device for 30 minutes, and control the temperature at 10-35°C; centrifuge the black suspension after ultrasonication, wash thoroughly, and dry at 80°C for 6 hours to obtain CMS / MnO 2 Material. Add 0.4g of p-toluenesulfonic acid into 30mL of absolute ethanol and stir evenly, then add 0.05g of pyrrole into the above solution, stir for 10...
Embodiment 2
[0061] Put 4g of glucose and 40mL of distilled water into a 50mL stainless steel reactor with built-in polytetrafluoroethylene, react at 180°C for 12h, then cool, centrifuge, wash thoroughly, and then dry at 60°C for 6h to obtain the carbon microsphere material; Add 0.05g of the carbon microsphere material prepared above, add 10mL of distilled water, and sonicate for 10min; weigh 0.25g of potassium permanganate, add it to the above mixed solution, stir to make it fully dissolve; then place it in an ultrasonic cleaning machine with an ultrasonic power of 400W Sonicate in the device for 60 minutes, and control the temperature at 10-35°C; centrifuge the black suspension after ultrasonication, wash thoroughly, and dry at 80°C for 6 hours to obtain CMS / MnO 2 Material. Add 0.3g of p-toluenesulfonic acid into 30mL of absolute ethanol and stir evenly, then add 0.03g of pyrrole into the above solution, stir for 10min, and record it as solution A; add 0.04g of ammonium persulfate into 2...
Embodiment 3
[0063] Put 4g of glucose and 40mL of distilled water into a 50mL stainless steel reactor with built-in polytetrafluoroethylene, react at 180°C for 15h, then cool, centrifuge, wash thoroughly, and then dry at 60°C for 6h to obtain the carbon microsphere material; Add 0.01g of the carbon microsphere material prepared above, add 10mL of distilled water, and ultrasonicate for 10min; weigh 0.1g of potassium permanganate, add it to the above mixed solution, stir to make it fully dissolve; then place it in an ultrasonic cleaning machine with an ultrasonic power of 400W Sonicate in the device for 30 minutes, and control the temperature at 10-35°C; centrifuge the black suspension after ultrasonication, wash thoroughly, and dry at 80°C for 6 hours to obtain CMS / MnO 2 Material. Add 0.4g of p-toluenesulfonic acid into 30mL of absolute ethanol and stir evenly, then add 0.05g of pyrrole into the above solution, stir for 10min, and record it as solution A; add 0.04g of ammonium persulfate in...
PUM
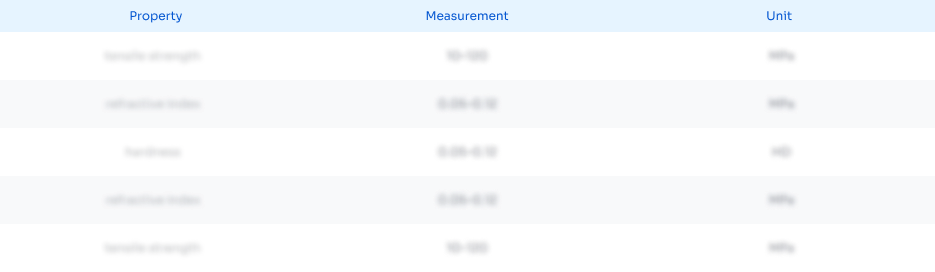
Abstract
Description
Claims
Application Information

- R&D
- Intellectual Property
- Life Sciences
- Materials
- Tech Scout
- Unparalleled Data Quality
- Higher Quality Content
- 60% Fewer Hallucinations
Browse by: Latest US Patents, China's latest patents, Technical Efficacy Thesaurus, Application Domain, Technology Topic, Popular Technical Reports.
© 2025 PatSnap. All rights reserved.Legal|Privacy policy|Modern Slavery Act Transparency Statement|Sitemap|About US| Contact US: help@patsnap.com