Optical fine measurement method based on parallel imaging
A parallel imaging and optical technology, applied in the field of optical measurement, can solve the problems of uncertain millimeter-level deviation, increase hardware cost, impact, etc., and achieve the effect of contrast enhancement, increased precision and accuracy
- Summary
- Abstract
- Description
- Claims
- Application Information
AI Technical Summary
Problems solved by technology
Method used
Image
Examples
Embodiment Construction
[0027] The present invention is further described below in conjunction with embodiment.
[0028] Such as figure 1 As shown, a method of optical fine measurement based on parallel imaging includes the following steps:
[0029] 1) The optical system of the whole lens is designed by combining the optical structure of the object-space telecentricity and the image-space telecentricity. The clear aperture of the diaphragm meets the telecentricity requirements of the entire optical system;
[0030] 2) Large depth of field with almost zero distortion:
[0031] The object telecentric structure can ensure that the lens has a larger depth of field when the object distance is fixed. Only the light rays parallel to the main optical axis on the object side of the lens are refracted by the optical system and then converged through the diaphragm. The object distance is guaranteed in the optical structure. The depth within the range of 160mm can be imaged and the distortion is less than 0.0...
PUM
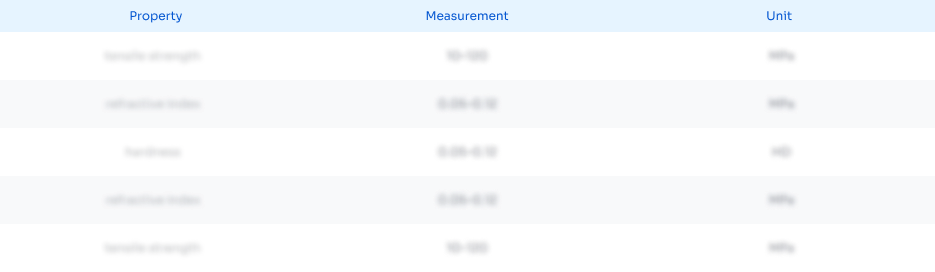
Abstract
Description
Claims
Application Information

- R&D
- Intellectual Property
- Life Sciences
- Materials
- Tech Scout
- Unparalleled Data Quality
- Higher Quality Content
- 60% Fewer Hallucinations
Browse by: Latest US Patents, China's latest patents, Technical Efficacy Thesaurus, Application Domain, Technology Topic, Popular Technical Reports.
© 2025 PatSnap. All rights reserved.Legal|Privacy policy|Modern Slavery Act Transparency Statement|Sitemap|About US| Contact US: help@patsnap.com