Double wet method flue gas desulphurization and dust removal treatment process
A wet flue gas desulfurization, desulfurization and dust removal technology, applied in gas treatment, separation methods, air quality improvement and other directions, can solve the problems of fog removal dead angle, regional structure blockage, low investment, etc., to reduce the moisture content of flue gas, reduce The final product, the effect of ultra-low emission
- Summary
- Abstract
- Description
- Claims
- Application Information
AI Technical Summary
Problems solved by technology
Method used
Image
Examples
Embodiment 1
[0061] Double-wet flue gas desulfurization and dust removal process, its structure includes: a first-level desulfurization and dust removal device for flue gas; a second-level desulfurization and dust removal device for second-level desulfurization and dust removal treatment A dedusting device; and an ammonia addition device externally connected to the secondary desulfurization and dedusting device and participating in ammonia desulfurization;
[0062] Wherein, the first-level desulfurization and dust removal device includes a Venturi dust removal tower 30, a first-level desulfurization water pool 1, a second-level desulfurization water pool 2, and a third-level desulfurization water pool 3, which constitute a desulfurization water pool and overflow and settle step by step. The first pumping pipeline 6 of the water supply of the Venturi dedusting tower 30 and the first return pipeline 7 connected between the water outlet of the Venturi dedusting tower 30 and the three-stage des...
Embodiment 2
[0067] The difference between this embodiment and embodiment 1 is:
[0068] The Venturi dedusting tower 30 of the first-stage desulfurization and dedusting device is connected to the external chain furnace 31 via the economizer 32; the flue gas generated by the combustion of the chain furnace 31 passes through the ammonia denitrification process in the furnace body and passes through the flue and the province. The coal container 32 enters the first-level desulfurization and dust removal treatment process; the ammonia denitrification treatment device includes: a calcium carbonate adding tank 29 is installed above the coal seam in the furnace body of the chain furnace, by which calcium carbonate is added above the coal seam; An ammonia water tank 28 for adding ammonia water or urea is installed in the high temperature zone where the temperature of the furnace body is greater than 200°C. The ammonia water tank 28 is connected with the external ammonia water tank 12 of the secondar...
experiment example
[0070] Material preparation:
[0071] Coal used in the test: low calorific value 5000cal / g; volatile matter 28.32%; total sulfur 0.6%; total water 13.25%;
[0072] Ammonia water with a concentration of 25%: 6T;
[0073] Limestone: 1 ton (200 mesh) Calcium oxide: 1 ton (calcium content > 80%) Magnesium oxide: 1 ton (magnesium content > 75%) Egg shell: 1 ton (calcium carbonate content > 80%)
[0074] Boiler model: chain grate quick-install hot water boiler (DZL4.2-1.0 / 110 / 70-AII);
[0075] Venturi dust removal tower: HSCL desulfurization water film dust collector (HSCL1-365T / H);
[0076] Clear water spray tower: adopt the clear water spray tower in embodiment 1
[0077] demister
[0078] Inspection instrument: WJ-60B pitot tube parallel automatic smoke and oil sampler (Qingdao Laoshan District Electronic Instrument Co., Ltd.).
[0079] Operation process: start the desulfurization water pump 8 connected to the primary desulfurization pool 1, start the dedusting water pump 10...
PUM
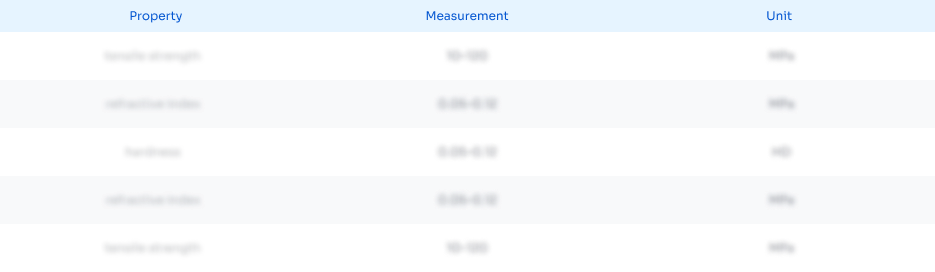
Abstract
Description
Claims
Application Information

- R&D
- Intellectual Property
- Life Sciences
- Materials
- Tech Scout
- Unparalleled Data Quality
- Higher Quality Content
- 60% Fewer Hallucinations
Browse by: Latest US Patents, China's latest patents, Technical Efficacy Thesaurus, Application Domain, Technology Topic, Popular Technical Reports.
© 2025 PatSnap. All rights reserved.Legal|Privacy policy|Modern Slavery Act Transparency Statement|Sitemap|About US| Contact US: help@patsnap.com