A friction-driven brake pad flatness detection mechanism
A flatness detection and friction-driven technology, applied in measurement devices, instruments, optical devices, etc., can solve the problems of slow detection speed and low efficiency, and achieve the effect of eliminating mechanical vibration, ensuring measurement accuracy and improving efficiency.
- Summary
- Abstract
- Description
- Claims
- Application Information
AI Technical Summary
Problems solved by technology
Method used
Image
Examples
Embodiment Construction
[0010] Below with the accompanying drawings ( figure 1 , figure 2 ) the present invention is described in further detail:
[0011] Installation: After fixing the pulley assemblies 1, 2, and 3 according to a certain degree of tension, attach the elastic body 14 to the outer surface of the timing belt 2, and install and fix the linear guide rail base 11 on both ends of the pulley at a certain distance. The first cylindrical guide rails 12 are respectively installed on both sides of the pulley assembly, and the highest surface of the cylindrical guide rails 12 is slightly higher than the plane of the synchronous belt 2, the column 4 is installed on the measurement base 10, and the crossbeam 9 is tightened by the sliding sleeve seat 5 and the sliding sleeve seat. The fastening screw 7 is installed on the column 4, and the laser displacement sensor 6 is installed below the beam 9 through the sensor fastening screw 8.
[0012] Adjustment: According to the range and accuracy requi...
PUM
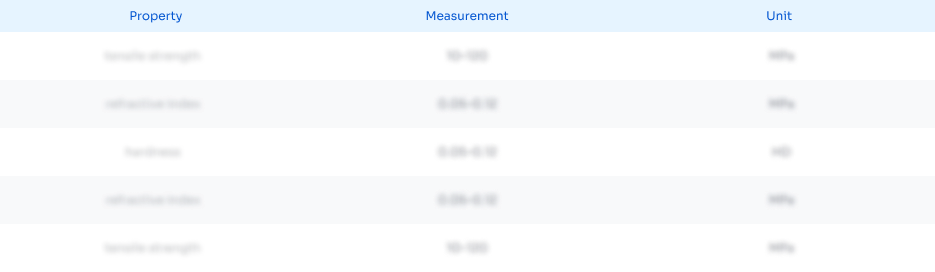
Abstract
Description
Claims
Application Information

- R&D
- Intellectual Property
- Life Sciences
- Materials
- Tech Scout
- Unparalleled Data Quality
- Higher Quality Content
- 60% Fewer Hallucinations
Browse by: Latest US Patents, China's latest patents, Technical Efficacy Thesaurus, Application Domain, Technology Topic, Popular Technical Reports.
© 2025 PatSnap. All rights reserved.Legal|Privacy policy|Modern Slavery Act Transparency Statement|Sitemap|About US| Contact US: help@patsnap.com