Preparation method of fresh non-dairy cream powder
A technology of fat-growing fresh cream and fresh cream, which is applied in the production/processing of edible oil/fat, edible oil/fat components, and preservation of edible oil/fat finished products, which can solve the problem of high transportation and storage conditions that affect product application , low temperature preservation and other issues, to achieve the effect of seasonal stability of product properties, convenient transportation, and four-season stability
- Summary
- Abstract
- Description
- Claims
- Application Information
AI Technical Summary
Problems solved by technology
Method used
Image
Examples
Embodiment 1
[0021] (1) Preparation of the oil phase: Weigh 500kg of hydrogenated palm kernel oil stripped of the carton and inner film, put it in a carburetor, turn on the steam valve to heat it to melt, and close the valve when the temperature reaches 60°C; add monoglyceride fat A total of 20kg of acid ester and diglyceride fatty acid ester, 60kg of diacetyl tartaric acid monoglyceride, stirred for 20 minutes and set aside.
[0022] (2) Preparation of water phase: Pour 60 kg of sodium caseinate, 20 kg of dipotassium hydrogen phosphate, and 3 kg of xanthan gum into deionized water, stir at high speed, and after fully dissolved, pass through a colloid mill to make it uniform and become a paste liquid.
[0023] (3) Mixing and shearing: First put 340kg of glucose syrup (dry basis) into the mixing tank, then put the paste liquid in step 2 and keep stirring, after a certain period of time, add the oil phase in step 1, add 1 kg of cream essence, stirring continuously to keep the temperature of...
Embodiment 2
[0029] (1) Preparation of the oil phase: Weigh 460kg of hydrogenated palm kernel oil stripped of the carton and inner film, put it into the oil pot, open the steam valve to heat it to melt, and close the valve when the temperature reaches 60°C; add monoglyceride fat A total of 15kg of acid ester and diglyceride fatty acid ester, 55kg of monoglyceride diacetyl tartrate, stirred for 20 minutes for subsequent use.
[0030] (2) Preparation of water phase: Pour 55kg of sodium caseinate, 18kg of dipotassium hydrogen phosphate, and 2kg of xanthan gum into deionized water, stir at high speed, and after fully dissolved, pass through a colloid mill to make it uniform and become a paste liquid.
[0031] (3) Mixing and shearing: first put 390kg of glucose syrup (dry basis) into the mixing tank, then put the paste liquid in step 2 and keep stirring, after a certain period of time, add the oil phase in step 1, add 1 kg of cream essence, stirring continuously to keep the temperature of the ...
Embodiment 3
[0037] (1) Preparation of the oil phase: Weigh 400kg of hydrogenated palm kernel oil stripped of the carton and inner film, put it in a carburetor, turn on the steam valve to heat it to melt, and close the valve when the temperature reaches 60°C; add monoglyceride fat A total of 10kg of acid ester and diglyceride fatty acid ester, 50kg of monoglyceride diacetyl tartrate, stirred for 20 minutes and set aside.
[0038] (2) Preparation of water phase: Pour 50kg of sodium caseinate, 10kg of dipotassium hydrogen phosphate, and 2kg of xanthan gum into deionized water, stir at high speed, and after fully dissolved, pass through a colloid mill to make it uniform and become a paste .
[0039] (3) Mixing and shearing: first put 478kg (dry basis) of glucose syrup into the mixing tank, then put the paste liquid in step 2 and keep stirring, after a certain period of time, add the oil phase in step 1, and keep stirring Stir to keep the feed liquid temperature at 50-70°C, and then use high-...
PUM
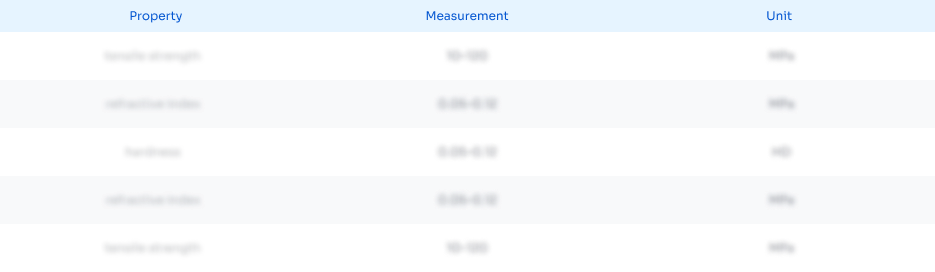
Abstract
Description
Claims
Application Information

- Generate Ideas
- Intellectual Property
- Life Sciences
- Materials
- Tech Scout
- Unparalleled Data Quality
- Higher Quality Content
- 60% Fewer Hallucinations
Browse by: Latest US Patents, China's latest patents, Technical Efficacy Thesaurus, Application Domain, Technology Topic, Popular Technical Reports.
© 2025 PatSnap. All rights reserved.Legal|Privacy policy|Modern Slavery Act Transparency Statement|Sitemap|About US| Contact US: help@patsnap.com