A stepper motor controller
A stepping motor and controller technology, applied in the direction of motor generator control, control system, electrical components, etc., can solve problems such as poor reliability, achieve the effects of realizing compression ratio, simplifying power supply lines, and simple control methods
- Summary
- Abstract
- Description
- Claims
- Application Information
AI Technical Summary
Problems solved by technology
Method used
Image
Examples
Embodiment Construction
[0027] The present invention is described in detail below in conjunction with accompanying drawing:
[0028] refer to figure 1 , the crankshaft, connecting rod and piston mechanism involved in the stepper motor controller of the present invention include a crankshaft 1, an annular graphite groove 2, a crankshaft graphite layout circuit 3, a brush 4, a brush 5, a connecting rod 6, a connecting rod Graphite layout circuit 7, electric brush 8, graphite layout circuit inside the piston 9, motor seat 10, piston internal wire 11, stepper motor (motor stator 12, motor rotor 14), piston 13, plug body lower part 15, guide plate 16, Inner sleeve 17, plug body top 18.
[0029] refer to figure 1 , the power supply line of the stepper motor controller of the present invention is completed by digging a graphite line on the crankshaft, connecting rod and piston, and the graphite line is insulated from the crankshaft, connecting rod and piston.
[0030] refer to figure 1 , figure 2 , ...
PUM
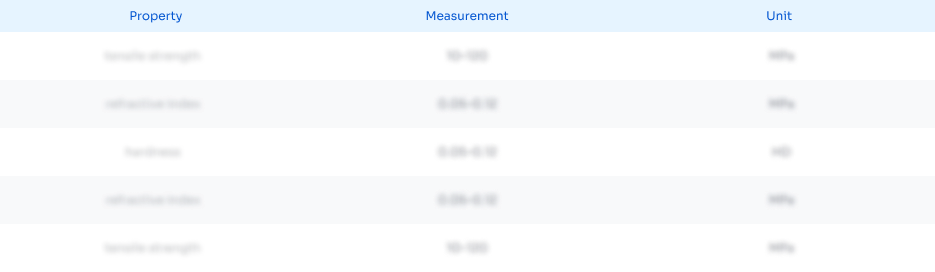
Abstract
Description
Claims
Application Information

- R&D Engineer
- R&D Manager
- IP Professional
- Industry Leading Data Capabilities
- Powerful AI technology
- Patent DNA Extraction
Browse by: Latest US Patents, China's latest patents, Technical Efficacy Thesaurus, Application Domain, Technology Topic, Popular Technical Reports.
© 2024 PatSnap. All rights reserved.Legal|Privacy policy|Modern Slavery Act Transparency Statement|Sitemap|About US| Contact US: help@patsnap.com