Earthquake control system of high-speed railway bridge
A technology for earthquake damage and high-speed railways, applied in bridges, bridge parts, bridge construction, etc., can solve the problems that the stirrups are difficult to effectively restrain the core concrete, cannot meet the seismic requirements, and it is difficult to form plastic hinges, so as to reduce the residual deformation after the earthquake , increase the repairability after the earthquake, and reduce the effect of residual deformation
- Summary
- Abstract
- Description
- Claims
- Application Information
AI Technical Summary
Problems solved by technology
Method used
Image
Examples
Embodiment Construction
[0029] Such as Figure 1 to Figure 4 A high-speed railway bridge earthquake damage control system shown includes: including, pier foundation, prefabricated shell wall composed of ECC and steel plates. Longitudinal reinforcement is arranged inside the prefabricated shell wall and concrete is poured, and unbonded prestressed reinforcement is vertically arranged along the pier. Two movable supports are set on the top of the pier to connect with the main girder. And 4 SMA coil springs are set between the top of the pier and the main girder.
[0030] The prefabricated shell walls composed of ECC and steel plates are arranged in sections along the pier height and connected by joints. The joints are toothed, which is convenient for the occlusion of the upper and lower prefabricated shell walls.
[0031] The unbonded prestressed tendons pass through the pier vertically, the bottom is anchored in the foundation, and the top is anchored in the upper part of the pier.
[0032] Studs ...
PUM
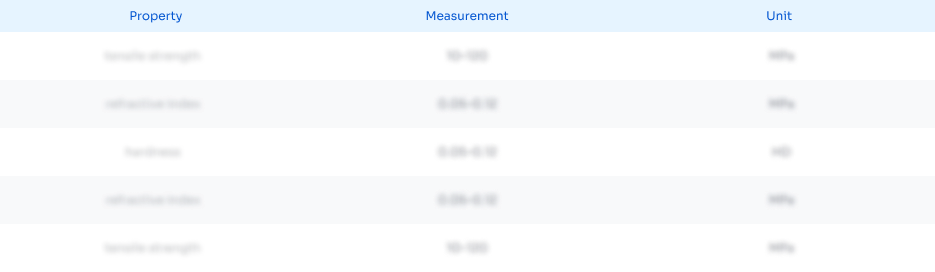
Abstract
Description
Claims
Application Information

- R&D Engineer
- R&D Manager
- IP Professional
- Industry Leading Data Capabilities
- Powerful AI technology
- Patent DNA Extraction
Browse by: Latest US Patents, China's latest patents, Technical Efficacy Thesaurus, Application Domain, Technology Topic, Popular Technical Reports.
© 2024 PatSnap. All rights reserved.Legal|Privacy policy|Modern Slavery Act Transparency Statement|Sitemap|About US| Contact US: help@patsnap.com