Efficient and porous MoS2-Zn hydrogen evolution electrode and preparation method thereof
A hydrogen evolution electrode, mos2-zn technology, applied in the direction of electrodes, electrode shapes/types, electrolytic coatings, etc., can solve the problems of industrial production difficulties, high energy consumption of hydrogen evolution electrodes, etc., to improve the shedding phenomenon, increase the real surface area and specific surface area , Improve the effect of hydrogen evolution activity
- Summary
- Abstract
- Description
- Claims
- Application Information
AI Technical Summary
Problems solved by technology
Method used
Image
Examples
Embodiment 1
[0034] (1) Pretreatment of conductive substrate
[0035]Nickel foam is selected as the substrate, and the nickel foam is cut to a size of 2.5cm·4.0cm, rinsed with deionized water and set aside. Firstly, electrolytic degreasing was performed on the tailored nickel foam; the nickel foam was used as the cathode and the anode successively, placed in the electrolyte, and electrolyzed for 15 minutes respectively, with a current density of 40mA cm -2 . The electrolyte formula is: sodium hydroxide 40g L -1 , sodium carbonate 25g·L -1 , sodium phosphate 25g·L -1 . After degreasing treatment, the electrode was rinsed repeatedly with deionized water until the pH value was neutral. Afterwards, pickling the foamed nickel after electrolytic degreasing: put it into the acid solution for 30 minutes, then rinse it with deionized water until the pH is neutral, and set it aside. The pickling liquid configuration method is to mix concentrated hydrochloric acid and deionized water according ...
Embodiment 2
[0049] Step (1) is the same as step (1) in Example 1;
[0050] (2) Composite electrodeposited MoS 2 -Zn coating
[0051] The conductive substrate processed in step (1) is the working electrode, and the nickel foam is the counter electrode;
[0052] The composition of the plating solution is: nickel sulfate 100g L -1 , zinc sulfate 20g·L -1 , anhydrous sodium acetate 5g·L -1 , sodium citrate 25g·L -1 , ammonium chloride 15g·L -1 , boric acid 15g·L -1 , nanometer molybdenum disulfide particles 10g L -1 ;
[0053] The temperature of the plating solution is 20°C, and the current density is 250mA·cm during the electroplating process. -2 , the deposition time is 30min.
[0054] During the electroplating process, in order to ensure that the molybdenum disulfide particles are uniformly dispersed in the deposition solution, magnetic stirring at a suitable speed is performed at the bottom of the electrolytic tank. Rinse with deionized water after electroplating to remove resi...
Embodiment 3
[0064] Step (1) is the same as step (1) in Example 1;
[0065] (2) Composite electrodeposited MoS 2 -Zn coating
[0066] The conductive substrate processed in step (1) is the working electrode, and the nickel foam is the counter electrode;
[0067] The composition of the plating solution is: nickel sulfate 120g L -1 , zinc sulfate 20g·L -1 , anhydrous sodium acetate 25g·L -1 , sodium citrate 20g·L -1 , ammonium chloride 15g·L -1 , boric acid 15g·L -1 , nano molybdenum disulfide particles 2g L -1 ;
[0068] The temperature of the plating solution is 25°C, and the current density is 400mA·cm during the electroplating process. -2 , the deposition time is 40min.
[0069] During the electroplating process, in order to ensure that the molybdenum disulfide particles are uniformly dispersed in the deposition solution, magnetic stirring at a suitable speed is performed at the bottom of the electrolytic tank. Rinse with deionized water after electroplating to remove residual ...
PUM
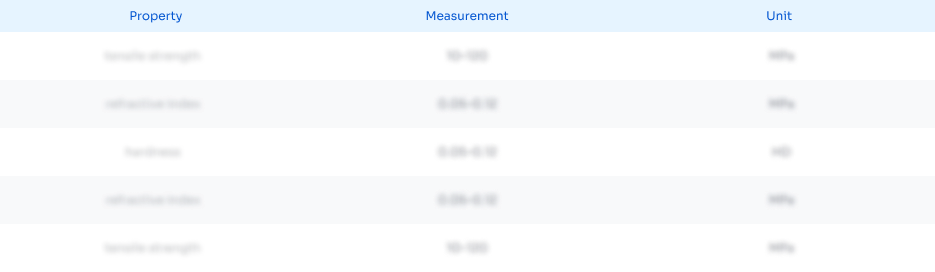
Abstract
Description
Claims
Application Information

- R&D Engineer
- R&D Manager
- IP Professional
- Industry Leading Data Capabilities
- Powerful AI technology
- Patent DNA Extraction
Browse by: Latest US Patents, China's latest patents, Technical Efficacy Thesaurus, Application Domain, Technology Topic, Popular Technical Reports.
© 2024 PatSnap. All rights reserved.Legal|Privacy policy|Modern Slavery Act Transparency Statement|Sitemap|About US| Contact US: help@patsnap.com