Hot-isostatic-pressing forming method for in-situ generation of continuous spatial net structure
A technology of hot isostatic pressing and in-situ reaction, which is applied in the field of advanced manufacturing and manufacturing aerospace, can solve problems such as difficult to meet performance requirements, achieve strong operability and applicability, and improve the effect of tensile strength
- Summary
- Abstract
- Description
- Claims
- Application Information
AI Technical Summary
Problems solved by technology
Method used
Image
Examples
example 1
[0037] This is an example for using the present invention to manufacture enhanced Ti6Al4V casing part wear resistance and tensile strength:
[0038] Ti6Al4V is a near-alpha titanium alloy, which is widely used in aerospace due to its ultra-high specific strength and excellent corrosion resistance, but its low wear resistance directly restricts its application range. In order to solve the defect of poor wear resistance of Ti6Al4V matrix material, this example chooses TiB 2 As a coating material, under the action of hot isostatic pressing at high temperature and high pressure, Ti and B will react in situ to form TiB and TiB 2 , TiB will grow into the adjacent powder during the generation process, enhancing the metallurgical bonding between powder and powder, thereby enhancing the tensile strength of the matrix; TiB 2 It is a ceramic material with high hardness, which can increase the hardness of the matrix material, thereby improving the wear resistance of the matrix material; ...
example 2
[0050] Using the present invention to manufacture enhanced plasticity and hardness of Ti6Al4V cylindrical parts is an example. Titanium alloys with cylindrical structures have typical engineering applications, such as missile casings, compressor casings in engines, and ship piping systems. Such key components usually have harsh working environments, and higher plasticity and hardness requirements are put forward for titanium alloy materials. To solve the above problems, the present invention uses Ti6Al4V as the matrix powder material and Ni as the reinforcing material. Under high pressure, Ti in the matrix will react with Ni atoms in situ to form TiNi, TiNi 2 , where TiNi belongs to the memory alloy, has super plasticity, TiNi 2 It has high hardness, and the two are dispersed in the matrix material at the same time, which improves the plasticity of the matrix material and improves the hardness.
[0051] In this context, using the present invention to manufacture Ti6Al4V cylin...
example 3
[0061] Using the present invention to manufacture enhanced Ni718 turbine disc parts plasticity and strength is an example. More than 50% of the mass of modern gas turbine engines use superalloys, and the amount of nickel-based superalloys accounts for about 40% of the engine materials. Because nickel-based alloys have excellent comprehensive properties at medium and high temperatures and are suitable for working at high temperatures for a long time, nickel-based superalloys are often used as materials for engine hot-end parts (blades, turbine disks, combustion chambers, etc.). Because of its high service temperature, higher requirements are put forward for the high-temperature performance of nickel-based alloy materials. In view of the above problems, the present invention uses Ni718 as the matrix powder material and Ti as the reinforcing material to improve the high-temperature strength and wear resistance of the matrix material. performance, under the action of high temperat...
PUM
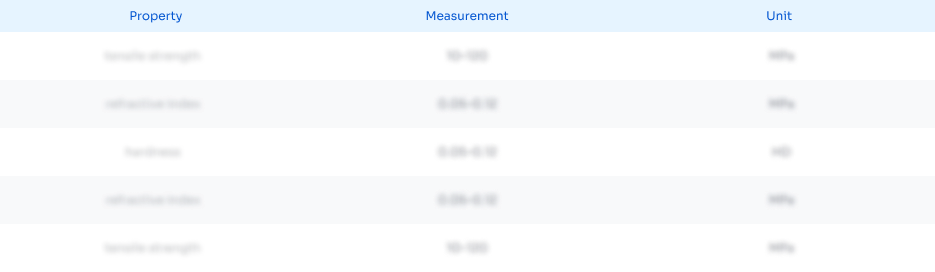
Abstract
Description
Claims
Application Information

- Generate Ideas
- Intellectual Property
- Life Sciences
- Materials
- Tech Scout
- Unparalleled Data Quality
- Higher Quality Content
- 60% Fewer Hallucinations
Browse by: Latest US Patents, China's latest patents, Technical Efficacy Thesaurus, Application Domain, Technology Topic, Popular Technical Reports.
© 2025 PatSnap. All rights reserved.Legal|Privacy policy|Modern Slavery Act Transparency Statement|Sitemap|About US| Contact US: help@patsnap.com