Automatic forming device for producing baking-free bricks
An automatic forming, non-burning brick technology, applied in the supply device, unloading device, forming indenter and other directions, can solve the problems of low continuous production, cumbersome processing process, etc., to achieve convenient operation, improve production efficiency, overall structure simple effect
- Summary
- Abstract
- Description
- Claims
- Application Information
AI Technical Summary
Problems solved by technology
Method used
Image
Examples
Embodiment 1
[0041] Such as Figure 1 ~ Figure 4 As shown, an automatic molding device for unburned brick production in this embodiment includes a frame 1, a blanking opening is provided on the frame 1, and a forming pushing mechanism 4 is arranged above the blanking opening. The material mechanism 4 is connected with the first hydraulic cylinder 3; a forming mechanism is arranged below the blanking port, and the forming mechanism is connected with the second hydraulic cylinder 6, specifically as figure 1 with figure 2 As shown, the falling hopper 2 above the frame 1 is used to place brick-making raw materials, the frame 1 is supported by legs 103 at the four corners, and the bottom of the legs 103 is provided with a fixed plate 104, and the area of the fixed plate 104 is much larger than that of the support. The cross-sectional area of the leg 103 significantly increases the support contact area between the leg 103 and the ground, which helps to enhance the stability of the whole se...
Embodiment 2
[0051] An automatic forming device for the production of non-fired bricks in this embodiment, its basic structure is the same as in Embodiment 1, furthermore, in this embodiment, the lower part of the bottom bracket 5 is connected with a fixed frame 502, and the second hydraulic cylinder 6 is located at In the frame surrounded by the bottom bracket 5 and the fixed frame 502, an adjustment mechanism for controlling the positional deviation of the second hydraulic cylinder 6 is arranged in the frame. Such as Figure 5 As shown, the bottom bracket 5 and the fixing frame 502 form a rectangular frame, and the adjustment mechanism includes adjusting screw rods 503 correspondingly arranged on the bottom brackets 5 on both sides, and fastening bolts 505 correspondingly arranged on the fixing brackets 502 on both sides. The end of the screw 503 is provided with a fastening block 504 close to the edge of the second hydraulic cylinder 6, and the side of the fastening block 504 in contact...
Embodiment 3
[0053] The basic structure of an automatic forming device for unburned brick production in this embodiment is the same as that in Embodiment 2. Furthermore, side fixing plates 101 are provided on both sides of the frame 1 in this embodiment to effectively strengthen the structural strength. , the guide pulley 102 is installed on the side fixing plate 101, one end of the support frame 202 is fixedly connected with the side fixing plate 101, and the other end is fixedly connected with the blanking hopper 2, as figure 1 As shown, the supporting frame 202 stably supports the dropping hopper 2 to improve its structural stability. Such as figure 2 As shown, two mounting frames 203 are fixedly connected to the side fixing plate 101, and one end of the two mounting frames 203 is fixedly connected to the blanking hopper 2 respectively, and a connecting rod 204 is arranged between the two mounting frames 203, and the vibrating device 205 is It is installed on the connecting rod 204 an...
PUM
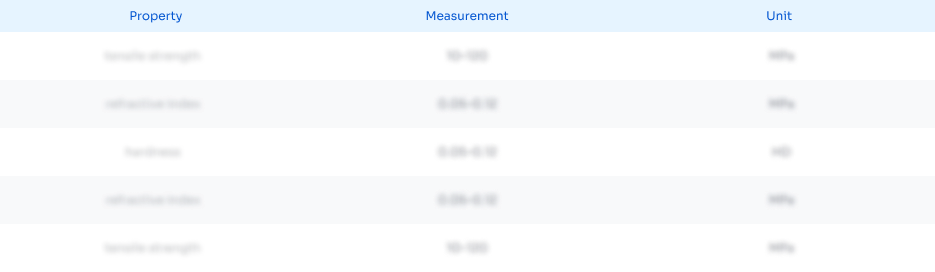
Abstract
Description
Claims
Application Information

- R&D
- Intellectual Property
- Life Sciences
- Materials
- Tech Scout
- Unparalleled Data Quality
- Higher Quality Content
- 60% Fewer Hallucinations
Browse by: Latest US Patents, China's latest patents, Technical Efficacy Thesaurus, Application Domain, Technology Topic, Popular Technical Reports.
© 2025 PatSnap. All rights reserved.Legal|Privacy policy|Modern Slavery Act Transparency Statement|Sitemap|About US| Contact US: help@patsnap.com