Method and device for measuring steel tube residual wall thickness magnetization pulse eddy current
A technology of pulsed eddy current and measurement method, which is applied in the direction of electromagnetic measuring device, measuring device, electric/magnetic thickness measurement, etc. It can solve the problems of difficulty in measuring the thickness of pipelines in service, insufficient stability and reliability, etc., and meet the requirements of clean state Low, simple structure, strong penetrating effect
- Summary
- Abstract
- Description
- Claims
- Application Information
AI Technical Summary
Problems solved by technology
Method used
Image
Examples
Embodiment Construction
[0026] The principles and features of the present invention are described below in conjunction with the accompanying drawings, and the examples given are only used to explain the present invention, and are not intended to limit the scope of the present invention.
[0027] The invention discloses a magnetization pulsed eddy current measurement method for the remaining wall thickness of a steel pipe, which comprises the following steps:
[0028] S1: Magnetize the inspected steel pipe 8 locally uniformly and reach a certain strength;
[0029] S2: The centerline of the exciting coil 31 and the magnetically sensitive direction of the receiving magnetic sensitive element 32 are facing the normal direction of the surface of the steel pipe 8, and the exciting coil 31 and the receiving magnetic sensitive element 32 form a pulsed eddy current measuring probe to sense the change of the magnetic permeability of the surface layer of the steel pipe 8;
[0030] S3: The plane of multiple puls...
PUM
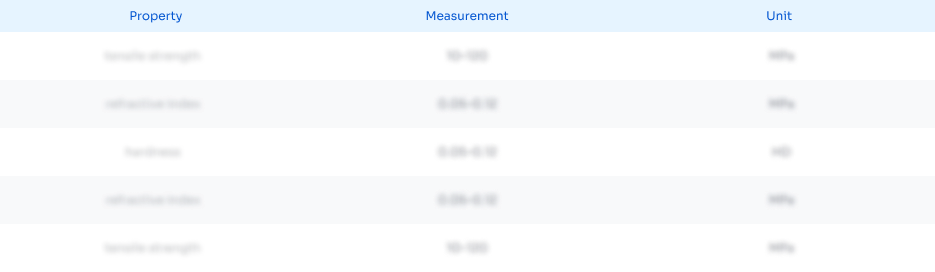
Abstract
Description
Claims
Application Information

- R&D Engineer
- R&D Manager
- IP Professional
- Industry Leading Data Capabilities
- Powerful AI technology
- Patent DNA Extraction
Browse by: Latest US Patents, China's latest patents, Technical Efficacy Thesaurus, Application Domain, Technology Topic, Popular Technical Reports.
© 2024 PatSnap. All rights reserved.Legal|Privacy policy|Modern Slavery Act Transparency Statement|Sitemap|About US| Contact US: help@patsnap.com