Hydraulic walking mechanism for tunnel lining working jumbo and control method
A technology for a template trolley and a traveling mechanism, which is applied to a transmission device with a rotating prime mover, etc., can solve the problems of reducing the walking reliability of the traveling device, unable to realize synchronous control, unable to realize continuous walking, etc., and achieves a small moment of inertia, The effect of good low speed stability and short start and stop times
- Summary
- Abstract
- Description
- Claims
- Application Information
AI Technical Summary
Problems solved by technology
Method used
Image
Examples
Embodiment Construction
[0025] The preferred technical solutions of the present invention will be described in detail below in conjunction with the accompanying drawings, but the protection scope of the present invention is not limited thereto.
[0026] The invention provides a hydraulic traveling mechanism and control method for a tunnel lining formwork trolley, and designs a hydraulic control circuit from a hydraulic pump station to a hydraulic motor and synchronous control of the left and right sides of the trolley walking frame in detail.
[0027] figure 1 Shown is the hydraulic principle structure diagram of the hydraulic traveling mechanism, including hydraulic pump station 1, proportional reversing valve I2, oil pressure sensor I3, hydraulic motor I4, encoder I5, proportional reversing valve II6, oil pressure sensor II7, hydraulic motor II8, encoder II9 and control unit 10, the hydraulic pump station 1, proportional reversing valve I2 and hydraulic motor I4 are sequentially connected through h...
PUM
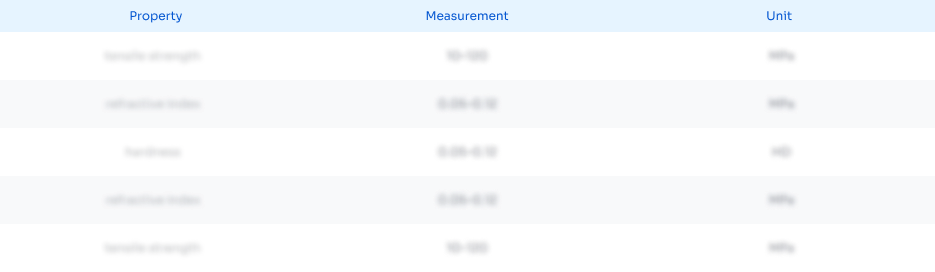
Abstract
Description
Claims
Application Information

- R&D
- Intellectual Property
- Life Sciences
- Materials
- Tech Scout
- Unparalleled Data Quality
- Higher Quality Content
- 60% Fewer Hallucinations
Browse by: Latest US Patents, China's latest patents, Technical Efficacy Thesaurus, Application Domain, Technology Topic, Popular Technical Reports.
© 2025 PatSnap. All rights reserved.Legal|Privacy policy|Modern Slavery Act Transparency Statement|Sitemap|About US| Contact US: help@patsnap.com