An aircraft long beam multi-position automatic fixture
A multi-station, long beam technology, used in manufacturing tools, workpiece clamping devices, clamping and other directions, can solve the problems of low flexibility and automation, poor reliability and stability, and low machining accuracy, and achieve improved reliability. The effect of improving the degree of automation and automation, improving processing accuracy, and improving production efficiency
- Summary
- Abstract
- Description
- Claims
- Application Information
AI Technical Summary
Problems solved by technology
Method used
Image
Examples
Embodiment Construction
[0025] The present invention will be further described below in conjunction with accompanying drawing.
[0026] Such as figure 1 , 2 , 5, 6, 7, 8, and 9, when the workpiece 36 is in the state of station 1, the bottom of the workpiece is jointly supported and positioned by the two inner support plates 55, 72, the end is positioned by the end baffle 41, and the side of the workpiece is positioned by the The outer baffle 101 is positioned and connected through the clamp body 1, and photoelectric sensors 2, 6, 14, 18, 20, 31, 32, 34, 37, 39, 40, 45, the photoelectric sensor is connected with the control device, and is used to detect whether the workpiece is completely positioned to realize accurate positioning of the workpiece, and the clamping cylinders 4, 8, 12, 16, 23, 28 are provided with pressure plates 3, 7, 11, 15, 22, 29, and are connected through the base of the cylinder for clamping the workpiece. Pressure sensors 5, 9, 13, 17, 21, 30 are arranged in the pressure plate...
PUM
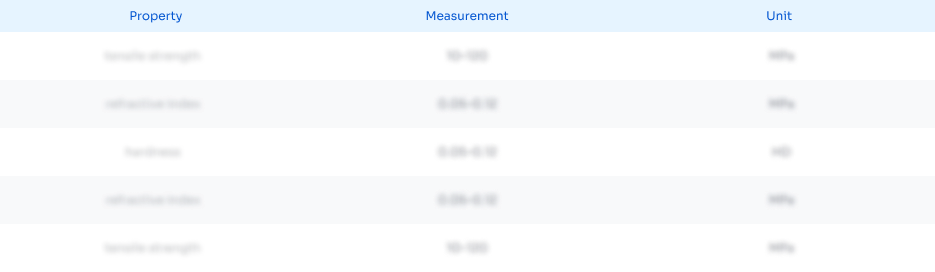
Abstract
Description
Claims
Application Information

- R&D Engineer
- R&D Manager
- IP Professional
- Industry Leading Data Capabilities
- Powerful AI technology
- Patent DNA Extraction
Browse by: Latest US Patents, China's latest patents, Technical Efficacy Thesaurus, Application Domain, Technology Topic, Popular Technical Reports.
© 2024 PatSnap. All rights reserved.Legal|Privacy policy|Modern Slavery Act Transparency Statement|Sitemap|About US| Contact US: help@patsnap.com