A compound insert for turning and milling with wave-shaped chip guide for heavy-duty cutting
A technology of inserts and waveforms, applied in cutting inserts, milling cutting inserts, tools for lathes, etc., can solve the problems of difficult chip breaking, low work efficiency, tool failure, etc., to increase the effective heat dissipation area and reduce contact. area, the effect of reducing the cutting temperature
- Summary
- Abstract
- Description
- Claims
- Application Information
AI Technical Summary
Problems solved by technology
Method used
Image
Examples
specific Embodiment approach 1
[0024] Specific implementation mode one: as figure 1 and figure 2 As shown, a compound insert for turning and milling with waveform chip guide for heavy-duty cutting, the shape of the insert 11 is a positive quadrangular truncated shape, and the four straight outer edges of the rake face 12 of the insert 11 are all processed with negative chamfering cutting edges 5 , the rake face 12 of the blade 11 is respectively provided with a triangular reinforcing protrusion 1 with a slope near the four tool tips, and the rake face 12 of the blade 11 is respectively provided near the four negative chamfer cutting edges 5 There are a plurality of strip-shaped protrusions 4 and a plurality of spherical protrusions 3, a square boss 13 is provided in the middle area of the rake face 12 of the blade 11, and a fastening screw is arranged on the geometric center of the square boss 13 The four sides of the hole 8 and the square boss 13 are wave-shaped chip guide surfaces 2 with a slope, and ...
specific Embodiment approach 2
[0027] Specific implementation mode two: as figure 1 As shown in the specific embodiment 1, a compound insert for heavy-duty cutting with wave-shaped chip guide turning and milling, the rake face 12 of the insert 11 is provided with a plurality of strips near the four negative chamfer cutting edges 5 The shape protrusion 4 and the plurality of spherical protrusions 3 are arranged symmetrically with respect to the cross center line of the blade 11 respectively.
specific Embodiment approach 3
[0028] Specific implementation mode three: as figure 1 As shown in the specific embodiment 1 or 2, a compound insert for heavy-duty cutting with wave-shaped chip guide turning and milling, the four cutting edges of the cutting edge 11 are respectively provided with a cutting edge arc transition edge 6 .
PUM
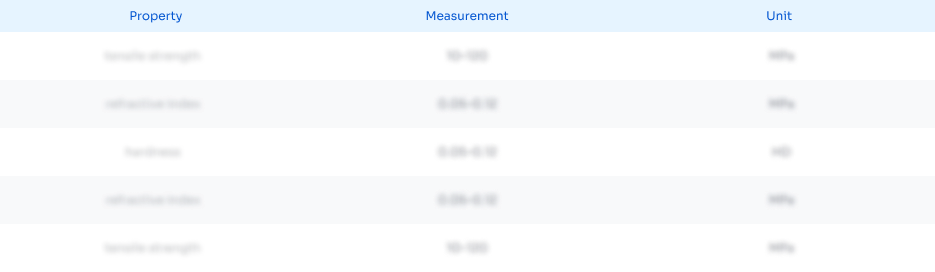
Abstract
Description
Claims
Application Information

- Generate Ideas
- Intellectual Property
- Life Sciences
- Materials
- Tech Scout
- Unparalleled Data Quality
- Higher Quality Content
- 60% Fewer Hallucinations
Browse by: Latest US Patents, China's latest patents, Technical Efficacy Thesaurus, Application Domain, Technology Topic, Popular Technical Reports.
© 2025 PatSnap. All rights reserved.Legal|Privacy policy|Modern Slavery Act Transparency Statement|Sitemap|About US| Contact US: help@patsnap.com