Preparation method of low molecular weight polyether polyol for polyether amine
A low-molecular-weight polyether and polyether polyol technology, which is used in the preparation of ethers, the preparation of ethers from alkylene oxide, and organic chemistry, can solve the problems of unstable product quality, wide molecular weight distribution, and low amine end capping rate. Strong bending resistance, improved amine value, good mutual solubility
- Summary
- Abstract
- Description
- Claims
- Application Information
AI Technical Summary
Problems solved by technology
Method used
Image
Examples
Embodiment 1
[0027] Add 270g of 2-methyl-1,3-propanediol and 2.4g of sodium hydroxide into a 2.5L autoclave at room temperature, evacuate to -0.09MPa and replace with nitrogen three times, start stirring and raise the temperature to 80°C. Under the vacuum degree of -0.09MPa, 150g of epoxides were continuously added dropwise, including 30g of propylene oxide and 120g of ethylene oxide. The pressure in the reaction kettle is ≤0.4MPa, the reaction temperature is 80-95°C, and the aging reaction is continued for 1 hour after the feeding is completed to obtain the intermediate polyether polyol. Heat up to 100°C, then continuously add 180g of propylene oxide dropwise, continue to react for a period of time, control the reaction temperature at 100-120°C, and the reaction pressure is ≤0.4MPa, wait until the pressure is stable and does not change for 30 minutes, then vacuumize the pressure ≤- Under 0.09MPa, the unreacted propylene oxide monomer is removed, and the polymerization reaction is complete...
Embodiment 2
[0029] Add 360g of 2-methyl-1,3-propanediol and 8.32g of potassium hydroxide into a 2.5L autoclave at room temperature, evacuate to -0.09MPa and replace with nitrogen three times, start stirring and raise the temperature to 80°C. Under the vacuum degree of -0.09MPa, 860g of epoxides were continuously added dropwise, including 420g of propylene oxide and 420g of ethylene oxide. The pressure in the reaction kettle is ≤0.4MPa, the reaction temperature is 80-95°C, and the aging reaction is continued for 1 hour after the feeding is completed to obtain the intermediate polyether polyol. Heat up to 100°C, then continuously drop 860g of propylene oxide, continue to react for a period of time, the reaction temperature is controlled at 100-120°C, the reaction pressure is ≤0.4MPa, wait until the pressure is stable and does not change for 30 minutes, and the vacuum pressure is ≤- Under 0.09MPa, the unreacted propylene oxide monomer is removed, and the polymerization reaction is completed....
Embodiment 3
[0031] Add 180g of 2-methyl-1,3-propanediol and 8g of potassium hydroxide into a 2.5L autoclave at room temperature, evacuate to -0.09MPa and replace with nitrogen three times, start stirring and raise the temperature to 80°C. Under the vacuum degree of -0.09MPa, 1229g of epoxide was added dropwise continuously, all of which were propylene oxide. The pressure in the reaction kettle is ≤0.4MPa, the reaction temperature is 80-95°C, and the aging reaction is continued for 1 hour after the feeding is completed to obtain the intermediate polyether polyol. Heat up to 100°C, then continuously drop 600g of propylene oxide, and continue to react for a period of time, the reaction temperature is controlled at 100-120°C, the reaction pressure is ≤0.4MPa, wait until the pressure is stable and does not change for 30 minutes, and the vacuum pressure is ≤- Under 0.09MPa, the unreacted propylene oxide monomer is removed, and the polymerization reaction is completed. Cool down to below 90°C, ...
PUM
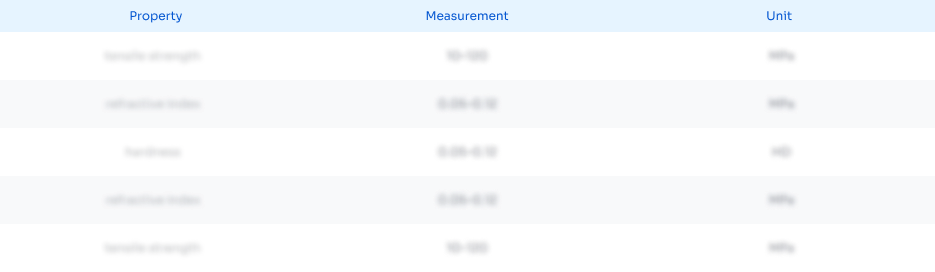
Abstract
Description
Claims
Application Information

- R&D
- Intellectual Property
- Life Sciences
- Materials
- Tech Scout
- Unparalleled Data Quality
- Higher Quality Content
- 60% Fewer Hallucinations
Browse by: Latest US Patents, China's latest patents, Technical Efficacy Thesaurus, Application Domain, Technology Topic, Popular Technical Reports.
© 2025 PatSnap. All rights reserved.Legal|Privacy policy|Modern Slavery Act Transparency Statement|Sitemap|About US| Contact US: help@patsnap.com