Precoated sand for casting instruments
A technology of coated sand and instruments, applied in casting molding equipment, molds, manufacturing tools, etc., can solve problems such as difficulty in meeting actual casting performance and high requirements for coated sand performance, achieve excellent casting performance, increase general The effect of adaptability and delaying the speed of gas generation
- Summary
- Abstract
- Description
- Claims
- Application Information
AI Technical Summary
Problems solved by technology
Method used
Examples
Embodiment 1
[0012] Embodiment 1: A coated sand for instrument casting, including the following raw materials in parts by weight: 1.5 parts of matrix resin, 0.04 parts of coupling agent, 0.4 parts of urotropine, 0.3 parts of curing agent, sulfonated lignin fiber 0.7 parts, 0.4 parts of montmorillonite powder, 15 parts of fused zircon sand, and 90 parts of magnesia.
Embodiment 2
[0013] Embodiment 2: A coated sand for instrument casting, including the following raw materials in parts by weight: 1 part of matrix resin, 0.02 part of coupling agent, 0.2 part of urotropine, 0.2 part of curing agent, sulfonated lignin fiber 0.5 parts, 0.2 parts of montmorillonite powder, 10 parts of fused zircon sand, and 80 parts of magnesia.
Embodiment 3
[0014] Embodiment 3: A coated sand for instrument casting, including the following raw materials in parts by weight: 2 parts of matrix resin, 0.06 part of coupling agent, 0.5 part of urotropine, 0.5 part of curing agent, sulfonated lignin fiber 1 part, 0.5 part of montmorillonite powder, 20 parts of fused zircon sand, 100 parts of magnesia.
PUM
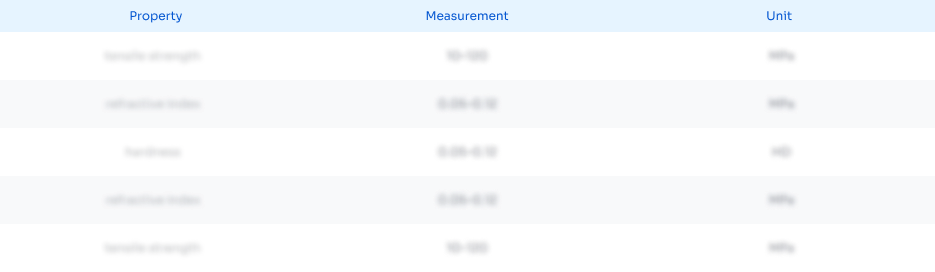
Abstract
Description
Claims
Application Information

- Generate Ideas
- Intellectual Property
- Life Sciences
- Materials
- Tech Scout
- Unparalleled Data Quality
- Higher Quality Content
- 60% Fewer Hallucinations
Browse by: Latest US Patents, China's latest patents, Technical Efficacy Thesaurus, Application Domain, Technology Topic, Popular Technical Reports.
© 2025 PatSnap. All rights reserved.Legal|Privacy policy|Modern Slavery Act Transparency Statement|Sitemap|About US| Contact US: help@patsnap.com