Subsequent filling method in medium and deep hole raise mining
A raised well and deep hole technology, applied in the direction of filling, ground mining, mining equipment, etc., can solve the problems of large cutting ratio, unsafe operation, low production efficiency, etc., and achieve large production capacity, fast well completion speed and high production efficiency high effect
- Summary
- Abstract
- Description
- Claims
- Application Information
AI Technical Summary
Problems solved by technology
Method used
Image
Examples
Embodiment Construction
[0022] The Basic Principle of the Subsequent Filling Method for Medium and Deep Hole Raise Mining in the Present Invention
[0023] For steeply inclined thin to medium-thick ore bodies, the ore blocks are arranged along the ore body trend and divided into stages in terms of vertical height; mining quasi-raises are arranged at both ends of the ore blocks, flat-bottomed mining structures are arranged at the bottom of the ore blocks, and a raise drilling rig is arranged at the upper part of the ore blocks Chamber; use raise drilling rigs to drill quasi-raised wells; use raise drilling rig lifting system to lift rock drilling and blasting work platforms; down-the-hole drilling rigs drill horizontal parallel or circular medium-deep holes from both sides of the raise well, concentrate rock drilling, and divide Blasting, concentrated ore extraction, and subsequent filling.
[0024] The specific operation steps of this method are as follows:
[0025] a) The ore blocks are arranged al...
PUM
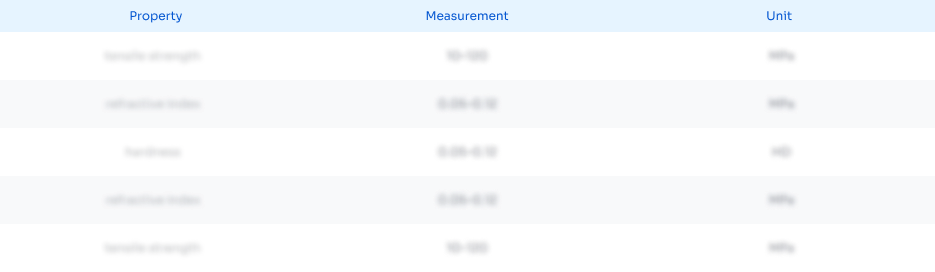
Abstract
Description
Claims
Application Information

- R&D Engineer
- R&D Manager
- IP Professional
- Industry Leading Data Capabilities
- Powerful AI technology
- Patent DNA Extraction
Browse by: Latest US Patents, China's latest patents, Technical Efficacy Thesaurus, Application Domain, Technology Topic, Popular Technical Reports.
© 2024 PatSnap. All rights reserved.Legal|Privacy policy|Modern Slavery Act Transparency Statement|Sitemap|About US| Contact US: help@patsnap.com