A dry dyeing method for superfine fiber synthetic leather without dyeing waste liquid
A technology of superfine fiber and dyeing method, which is applied in the direction of dyeing method, printing, printing device, etc. It can solve the problems of difficulty in meeting market requirements, restricting product development, and single product variety, so as to improve wet rubbing fastness and improve dyeing Effects of fastness and high molecular weight
- Summary
- Abstract
- Description
- Claims
- Application Information
AI Technical Summary
Problems solved by technology
Method used
Examples
Embodiment 1
[0027] Two three-plate printing machines in series are used as dyeing equipment, and the superfine fiber synthetic leather base cloth is dyed by roller coating printing; the specific dyeing method is as follows:
[0028] 1) The superfine fiber synthetic leather base cloth passes through the first three-plate printing machine, and at the first printing position and the second printing position, the emulsified dye is transferred to the superfine fiber synthetic leather base through the transfer action of the printing roller. On both sides of the cloth, the third printing position is squeezed by the printing roller and the support roller to make the dye completely penetrate, and then pass through the oven and dry at 120°C for 10 minutes;
[0029] Wherein, the superfine fiber synthetic leather base cloth is an island-fixed superfine fiber synthetic leather base cloth.
[0030]The emulsifying dye is prepared by the following method: in parts by weight, 10 parts of dye, 7 parts of e...
Embodiment 2
[0036] Two three-plate printing machines in series are used as dyeing equipment, and the superfine fiber synthetic leather base cloth is dyed by roller coating printing; the specific dyeing method is as follows:
[0037] 1) The superfine fiber synthetic leather base cloth passes through the first three-plate printing machine, and at the first printing position and the second printing position, the emulsified dye is transferred to the superfine fiber synthetic leather base through the transfer action of the printing roller. On both sides of the cloth, at the third printing position, the dye is completely infiltrated by the extrusion of the printing roller and the support roller, and then passed through the oven, and dried at 130°C for 7 minutes;
[0038] Wherein, the superfine fiber synthetic leather base cloth is non-island-fixed superfine fiber synthetic leather base cloth.
[0039] The emulsifying dye is prepared by the following method: in parts by weight, 20 parts of dyes,...
Embodiment 3
[0045] Two three-plate printing machines in series are used as dyeing equipment, and the superfine fiber synthetic leather base cloth is dyed by roller coating printing; the specific dyeing method is as follows:
[0046] 1) The superfine fiber synthetic leather base cloth passes through the first three-plate printing machine, and at the first printing position and the second printing position, the emulsified dye is transferred to the superfine fiber synthetic leather base through the transfer action of the printing roller. Both sides of the cloth, in the third printing position, pass the pressing action of the printing roller and the support roller to make the dye completely penetrate, and then pass through the oven and dry at 150 ° C for 5 minutes;
[0047] Wherein, the superfine fiber synthetic leather base cloth is a pie-shaped superfine fiber synthetic leather base cloth.
[0048] The emulsifying dye is prepared by the following method: in parts by weight, 13 parts of dyes...
PUM
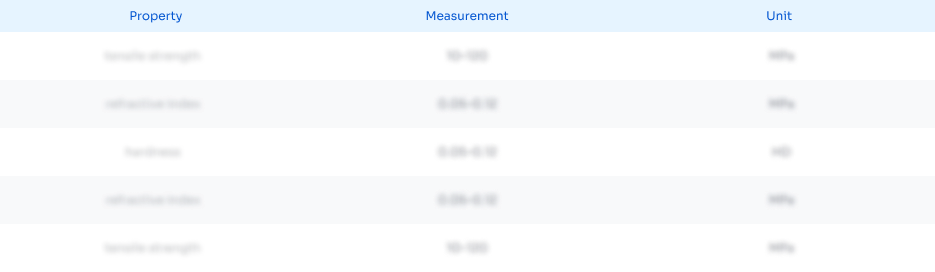
Abstract
Description
Claims
Application Information

- R&D
- Intellectual Property
- Life Sciences
- Materials
- Tech Scout
- Unparalleled Data Quality
- Higher Quality Content
- 60% Fewer Hallucinations
Browse by: Latest US Patents, China's latest patents, Technical Efficacy Thesaurus, Application Domain, Technology Topic, Popular Technical Reports.
© 2025 PatSnap. All rights reserved.Legal|Privacy policy|Modern Slavery Act Transparency Statement|Sitemap|About US| Contact US: help@patsnap.com