Jun-porcelain wood burning glaze
A Jun porcelain and firewood firing technology, which is applied in the field of Jun porcelain firewood glaze, can solve the problems of uneven color and low yield of Jun porcelain, achieve uniform and moist glaze color, reduce melting temperature and high temperature viscosity, reduce melting temperature and The effect of the coefficient of expansion
- Summary
- Abstract
- Description
- Claims
- Application Information
AI Technical Summary
Problems solved by technology
Method used
Examples
Embodiment 1
[0017] A firewood glaze for Jun porcelain, which is composed of the following components in parts by weight: 28 parts of quartz, 19 parts of potassium feldspar, 7 parts of albite, 15 parts of plant ash, 10 parts of limestone, 3 parts of talc and 1 part of iron oxide share.
[0018] The manufacturing process of making Jun porcelain with the described Jun porcelain firewood glaze comprises the following steps:
[0019] Step 1: use a ball mill with a rotating speed of 300r / min to wet ball mill the above-mentioned various raw materials for 2 hours, pass through a 100-mesh sieve, and obtain Jun porcelain glaze slurry;
[0020] Step 2: The body is bisque fired at 500°C and dried, and the Jun porcelain glaze slurry in step 1 is applied to the dried body to obtain a glazed body with a thickness of 1mm;
[0021] Step 3: Put the dried glazed body into a wood kiln for firing, control the temperature of the wood kiln at a rate of 130°C per hour for glaze firing, wait until the temperatur...
Embodiment 2
[0024] A firewood glaze for Jun porcelain, which is composed of the following components in parts by weight: 29 parts of quartz, 21 parts of potassium feldspar, 8 parts of albite, 16 parts of plant ash, 12 parts of limestone, 3 parts of talc and 1 part of iron oxide share.
[0025] The manufacturing process of making Jun porcelain with the described Jun porcelain firewood glaze comprises the following steps:
[0026] Step 1: use a ball mill with a rotating speed of 300r / min to wet ball mill the above-mentioned various raw materials for 2 hours, pass through a 100-mesh sieve, and obtain Jun porcelain glaze slurry;
[0027] Step 2: The green body is biscuit fired at 500°C and dried, and the Jun porcelain glaze slurry in step 1 is applied to the dried green body to obtain a glazed green body with a glaze layer thickness of 1.3 mm;
[0028] Step 3: Put the dried glazed body into a wood kiln for firing, control the temperature of the wood kiln at a rate of 150°C per hour for glaze...
Embodiment 3
[0031] A firewood glaze for Jun porcelain, which is composed of the following components in parts by weight: 35 parts of quartz, 23 parts of potassium feldspar, 12 parts of albite, 18 parts of plant ash, 15 parts of limestone, 4 parts of talc and 2 parts of iron oxide share.
[0032] The manufacturing process of making Jun porcelain with the described Jun porcelain firewood glaze comprises the following steps:
[0033] Step 1: use a ball mill with a rotating speed of 300r / min to wet ball mill the above-mentioned various raw materials for 2 hours, pass through a 100-mesh sieve, and obtain Jun porcelain glaze slurry;
[0034] Step 2: The green body is bisque fired at 500°C and dried, and the Jun porcelain glaze slurry in step 1 is applied to the dried green body to obtain a glazed green body with a glaze layer thickness of 1.8mm;
[0035] Step 3: Put the dried glazed body into a firewood kiln for firing, control the temperature of the firewood kiln at a rate of 180°C per hour f...
PUM
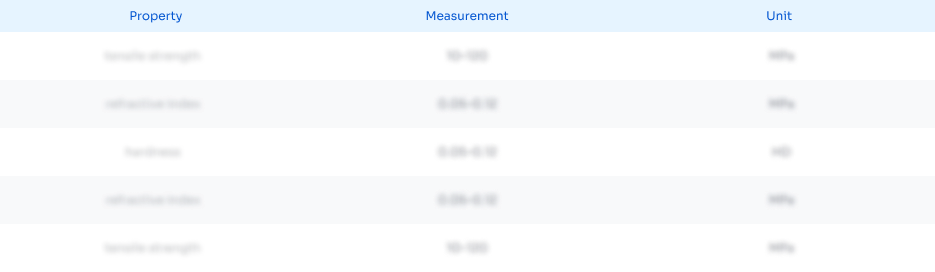
Abstract
Description
Claims
Application Information

- Generate Ideas
- Intellectual Property
- Life Sciences
- Materials
- Tech Scout
- Unparalleled Data Quality
- Higher Quality Content
- 60% Fewer Hallucinations
Browse by: Latest US Patents, China's latest patents, Technical Efficacy Thesaurus, Application Domain, Technology Topic, Popular Technical Reports.
© 2025 PatSnap. All rights reserved.Legal|Privacy policy|Modern Slavery Act Transparency Statement|Sitemap|About US| Contact US: help@patsnap.com