Method for calculating thermal expansion coefficient of composite plate based on optical fiber strain conversion matrix
A composite material plate and thermal expansion coefficient technology, applied in the direction of material thermal expansion coefficient, can solve the problems of lateral strain deviation, affecting measurement accuracy, reducing measurement accuracy, etc.
- Summary
- Abstract
- Description
- Claims
- Application Information
AI Technical Summary
Problems solved by technology
Method used
Image
Examples
Embodiment Construction
[0067] The present invention will be further described below in conjunction with the accompanying drawings.
[0068] A method for calculating the thermal expansion coefficient of a composite material plate based on an optical fiber strain transfer matrix, comprising the following steps:
[0069] Step 1. Definition of the coordinate system of the composite material surface and the layout of the fiber Bragg grating sensor network and the establishment of the fiber FBG coordinate system; the fiber Bragg grating sensor network includes two mutually perpendicular fiber Bragg grating sensors FBG1, FBG2 and a freely placed temperature compensation grating sensor FBG3;
[0070] Two fiber grating sensors FBG1 and FBG2 perpendicular to each other are respectively pasted on the surface of the composite material board structure to be tested. Establish two three-dimensional Cartesian coordinate systems, such as figure 1 As shown, they are: the optical fiber FBG coordinate system, with FB...
PUM
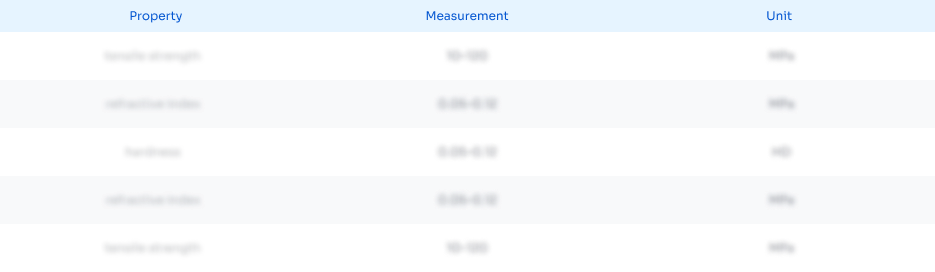
Abstract
Description
Claims
Application Information

- R&D
- Intellectual Property
- Life Sciences
- Materials
- Tech Scout
- Unparalleled Data Quality
- Higher Quality Content
- 60% Fewer Hallucinations
Browse by: Latest US Patents, China's latest patents, Technical Efficacy Thesaurus, Application Domain, Technology Topic, Popular Technical Reports.
© 2025 PatSnap. All rights reserved.Legal|Privacy policy|Modern Slavery Act Transparency Statement|Sitemap|About US| Contact US: help@patsnap.com