A method of reducing oxalate formation during oxygen delignification
A technology of oxygen delignification and medium oxalate, which is applied in the field of pulp and paper making, can solve the problems of complicated operation, long time consumption, and reduced production efficiency, and achieve the effects of simple operation, improved pulp properties, and reduced consumption
- Summary
- Abstract
- Description
- Claims
- Application Information
AI Technical Summary
Problems solved by technology
Method used
Image
Examples
Embodiment 1
[0027] Eucalyptus kraft pulp
[0028] (1) Sodium phytate combined with ultrasonic treatment
[0029] Add sodium phytate (20kg / t absolute dry pulp) to the pulp, adjust the pulp concentration to 10%, perform ultrasonic treatment for 60 minutes after mixing evenly, the ultrasonic power is 200W, and the treatment temperature is 50°C, and the pulp is washed after treatment.
[0030] (2) Oxygen delignification
[0031] Add sodium hydroxide (10kg / t absolute dry pulp) and magnesium hydroxide (10kg / t absolute dry pulp) to the treated eucalyptus kraft pulp, adjust the pulp concentration to 10%, and introduce oxygen for oxygen delignification The oxygen delignification temperature is 100° C., the oxygen pressure is 0.8 MPa, and the time is 60 minutes. After the end, the pulp is washed.
[0032] Experimental results:
[0033]
Embodiment 2
[0035] Bamboo Kraft Pulp
[0036] (1) Sodium phytate combined with ultrasonic treatment
[0037] Add sodium phytate (10kg / t absolute dry pulp) to the pulp, adjust the pulp concentration to 10%, perform ultrasonic treatment for 45min after mixing evenly, the ultrasonic power is 500W, and the treatment temperature is 30°C, and the pulp is washed after treatment.
[0038] (2) Oxygen delignification
[0039] Add sodium hydroxide (15kg / t absolute dry pulp) and magnesium hydroxide (5kg / t absolute dry pulp) to the treated bamboo sulfate pulp, adjust the pulp concentration to 10%, and feed oxygen to carry out oxygen delignification , the oxygen delignification temperature is 100° C., the oxygen pressure is 0.8 MPa, and the time is 60 minutes. After the end, the pulp is washed.
[0040] Experimental results:
[0041]
Embodiment 3
[0043] Acacia kraft pulp
[0044] (1) Sodium phytate combined with ultrasonic treatment
[0045] Add sodium phytate (25kg / t absolute dry pulp) to the pulp, adjust the pulp concentration to 10%, perform ultrasonic treatment for 120min after mixing evenly, the ultrasonic power is 500W, and the treatment temperature is 50°C, and the pulp is washed after treatment.
[0046] (2) Oxygen delignification
[0047] Add sodium hydroxide (10kg / t absolute dry pulp) and magnesium hydroxide (15kg / t absolute dry pulp) to the treated acacia kraft pulp, adjust the pulp concentration to 10%, and introduce oxygen for oxygen delignification The oxygen delignification temperature is 100° C., the oxygen pressure is 0.8 MPa, and the time is 60 minutes. After the end, the pulp is washed.
[0048] Experimental results:
[0049]
PUM
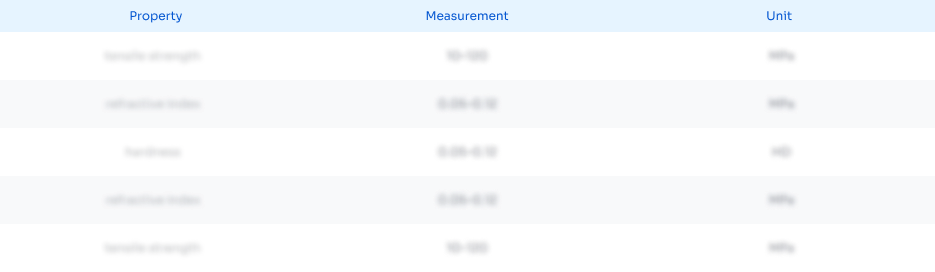
Abstract
Description
Claims
Application Information

- R&D
- Intellectual Property
- Life Sciences
- Materials
- Tech Scout
- Unparalleled Data Quality
- Higher Quality Content
- 60% Fewer Hallucinations
Browse by: Latest US Patents, China's latest patents, Technical Efficacy Thesaurus, Application Domain, Technology Topic, Popular Technical Reports.
© 2025 PatSnap. All rights reserved.Legal|Privacy policy|Modern Slavery Act Transparency Statement|Sitemap|About US| Contact US: help@patsnap.com