Manufacturing method for composite hub
A technology of composite materials and manufacturing methods, applied in household appliances, other household appliances, household components, etc., can solve problems such as complex shapes, inability to manufacture structural performance requirements, low fiber content, etc.
- Summary
- Abstract
- Description
- Claims
- Application Information
AI Technical Summary
Problems solved by technology
Method used
Image
Examples
Embodiment 1
[0022] Embodiment 1 manufactures carbon / epoxy composite material wheel hub
[0023] 1. Fabrication of Preforms
[0024] 1) The overall hub structure ( figure 2 As shown in (a), it is divided into three sub-structures according to the lay-up and process requirements of the product ( figure 2 Shown in (b), (c), and (d)) as the preform model, design and manufacture the mold according to the preform model, and pre-cut the reinforcement material (T-700 carbon fiber and fabric) according to the requirements of the design layer; the preform The cut reinforcement material is placed in the designed and manufactured mold according to the design level requirements and order, and 2 grams of shaping glue is spread on each layer. After all layers are laid, the mold is clamped, heated and shaped, and the heating time is 2 hours. The temperature is 130 degrees, after cooling to room temperature, the exposed burrs are cut, and the wheel core preform (1), the spoke preform (2), and the rim ...
Embodiment 2
[0033] Embodiment 2 manufactures carbon / phenolic composite material hub
[0034] 1. Fabrication of Preforms
[0035] 1) The overall hub structure ( figure 2 As shown in (a), it is divided into three sub-structures according to the lay-up and process requirements of the product ( figure 2 Shown in (b), (c), and (d)) as the preform model, design and manufacture the mold according to the preform model, and pre-cut the reinforcement material (T-700 carbon fiber and fabric) according to the requirements of the design layer; the preform The cut reinforcement material is placed in the designed and manufactured mold according to the design level requirements and order, and 2 grams of shaping glue is spread on each layer. After all layers are laid, the mold is clamped, heated and shaped, and the heating time is 2 hours. The temperature is 130 degrees Celsius, after cooling to room temperature, the exposed burrs are cut and pressed into wheel core preforms (1), spoke preforms (2), a...
Embodiment 3
[0043] Example 3 Glass fiber / multi-component heterocyclic resin composite hub
[0044] 1. Fabrication of Preforms
[0045] 1) The overall hub structure ( figure 2 As shown in (a), it is divided into three sub-structures according to the lay-up and process requirements of the product ( figure 2 Shown in (b), (c), and (d)) as the preform model, design and manufacture the mold according to the preform model, and pre-cut the reinforcement material (T-700 carbon fiber and fabric) according to the requirements of the design layer; the preform The cut reinforcement material is placed in the designed and manufactured mold according to the design level requirements and order, and 2 grams of shaping glue is spread on each layer. After all layers are laid, the mold is clamped, heated and shaped, and the heating time is 2 hours. The temperature is 130 degrees Celsius, after cooling to room temperature, the exposed burrs are cut and pressed into wheel core preforms (1), spoke preforms ...
PUM
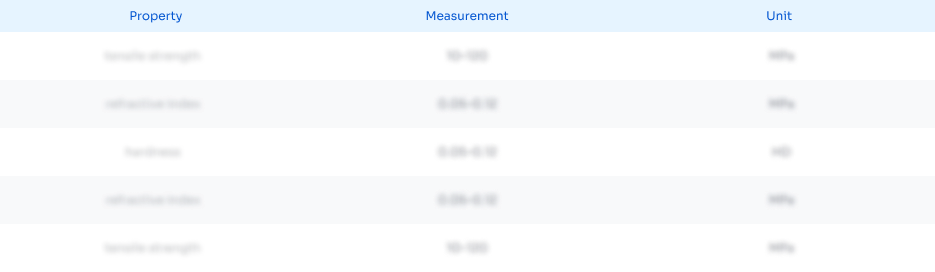
Abstract
Description
Claims
Application Information

- Generate Ideas
- Intellectual Property
- Life Sciences
- Materials
- Tech Scout
- Unparalleled Data Quality
- Higher Quality Content
- 60% Fewer Hallucinations
Browse by: Latest US Patents, China's latest patents, Technical Efficacy Thesaurus, Application Domain, Technology Topic, Popular Technical Reports.
© 2025 PatSnap. All rights reserved.Legal|Privacy policy|Modern Slavery Act Transparency Statement|Sitemap|About US| Contact US: help@patsnap.com