Sintering flue gas denitrifying agent and preparation method thereof
A technology for sintering flue gas and denitrification agent, applied in separation methods, chemical instruments and methods, gas treatment, etc., can solve the problems of easy loss of activity, long running time, low denitration efficiency, etc., and achieve the effect of reducing costs
- Summary
- Abstract
- Description
- Claims
- Application Information
AI Technical Summary
Problems solved by technology
Method used
Examples
Embodiment 1
[0019] A sintering flue gas denitration agent, calculated by weight percentage, includes the following raw materials:
[0020] 15% of sludge, 7% of fly ash, 0.8% of ammonium carbonate, 0.8% of lanthanum nitrate, 0.06% of phosphorus oxide, 20% of pyrolusite powder, and the balance is water
[0021] The preparation method comprises the following steps:
[0022] Weigh the sludge, fly ash, ammonium carbonate, lanthanum nitrate, pyrolusite powder and water according to the ratio, and then mix and stir until a viscous material is formed.
Embodiment 2
[0024] A sintering flue gas denitration agent, calculated by weight percentage, includes the following raw materials:
[0025] 10% of sludge, 5% of fly ash, 0.5% of ammonium bicarbonate, 0.5% of lanthanum nitrate, 0.02% of phosphorus oxide, 15% of pyrolusite powder, and the balance is water. .
[0026] The preparation method comprises the following steps:
[0027] Weigh the sludge, fly ash, ammonium bicarbonate, lanthanum nitrate, phosphorus oxide pyrolusite powder and water according to the ratio, and then mix and stir until a viscous material is formed.
Embodiment 3
[0029] A sintering flue gas denitration agent, calculated by weight percentage, includes the following raw materials:
[0030] 12% of sludge, 7% of fly ash, 0.8% of ammonium chloride, 0.6% of lanthanum nitrate, 0.04% of phosphorus oxide, 18% of pyrolusite powder, and the balance is water.
[0031] The preparation method comprises the following steps:
[0032] Weigh the sludge, fly ash, ammonium chloride, lanthanum nitrate, phosphorus oxide pyrolusite powder and water according to the ratio, and then mix and stir until a viscous material is formed.
PUM
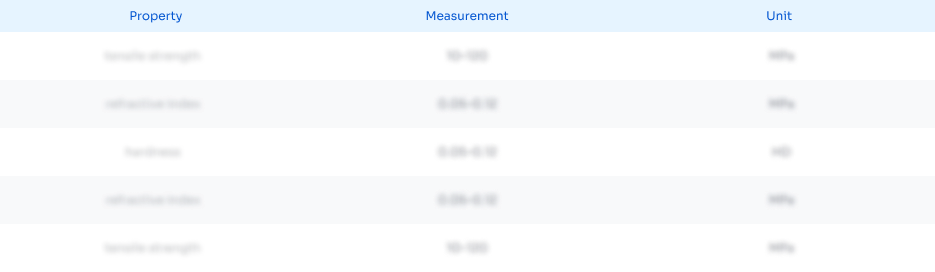
Abstract
Description
Claims
Application Information

- R&D
- Intellectual Property
- Life Sciences
- Materials
- Tech Scout
- Unparalleled Data Quality
- Higher Quality Content
- 60% Fewer Hallucinations
Browse by: Latest US Patents, China's latest patents, Technical Efficacy Thesaurus, Application Domain, Technology Topic, Popular Technical Reports.
© 2025 PatSnap. All rights reserved.Legal|Privacy policy|Modern Slavery Act Transparency Statement|Sitemap|About US| Contact US: help@patsnap.com