A tile slit filler
A technology for gaps and ceramic tiles, which is applied in the field of ceramic tile gap fillers. It can solve problems such as insufficient compatibility, unsatisfactory filling and reinforcing effects, poor dispersion, etc., and achieve good filling and reinforcing effects, high application value, and improved performance.
- Summary
- Abstract
- Description
- Claims
- Application Information
AI Technical Summary
Problems solved by technology
Method used
Examples
Embodiment 1
[0007] A ceramic tile gap filler is made from the following raw materials by weight: 200 parts of calcium carbonate, 20 parts of aluminum hydroxide, 20 parts of zeolite powder, 20 parts of kaolin, 20 parts of wollastonite, 20 parts of magnesium silicate, 20 parts of magnesium phosphate parts, 2 parts of bentonite, 1 part of sodium polyacrylate, 3 parts of triethanolamine, 2 parts of sodium tripolyphosphate, 2 parts of sodium polyacrylate, 1 part of formaldehyde resin, 1 part of polyaspartic acid, methyltriethoxysilane 1 serving.
[0008] The preparation method is that the above-mentioned raw materials are mixed uniformly and ground to 400 meshes.
Embodiment 2
[0010] A ceramic tile gap filler is made from the following raw materials by weight: 220 parts of calcium carbonate, 20 parts of aluminum hydroxide, 20 parts of zeolite powder, 20 parts of kaolin, 20 parts of wollastonite, 20 parts of magnesium silicate, 20 parts of magnesium phosphate parts, 2 parts of bentonite, 1 part of sodium polyacrylate, 3 parts of triethanolamine, 2 parts of sodium tripolyphosphate, 2 parts of sodium polyacrylate, 1 part of formaldehyde resin, 1 part of polyaspartic acid, methyltriethoxysilane 1 serving.
[0011] The preparation method is that the above-mentioned raw materials are mixed uniformly and ground to 400 meshes.
Embodiment 3
[0013] A ceramic tile gap filler is made from the following raw materials by weight: 230 parts of calcium carbonate, 20 parts of aluminum hydroxide, 20 parts of zeolite powder, 20 parts of kaolin, 20 parts of wollastonite, 20 parts of magnesium silicate, 20 parts of magnesium phosphate parts, 2 parts of bentonite, 1 part of sodium polyacrylate, 3 parts of triethanolamine, 2 parts of sodium tripolyphosphate, 2 parts of sodium polyacrylate, 1 part of formaldehyde resin, 1 part of polyaspartic acid, methyltriethoxysilane 1 serving.
[0014] The preparation method is that the above-mentioned raw materials are mixed uniformly and ground to 400 meshes.
PUM
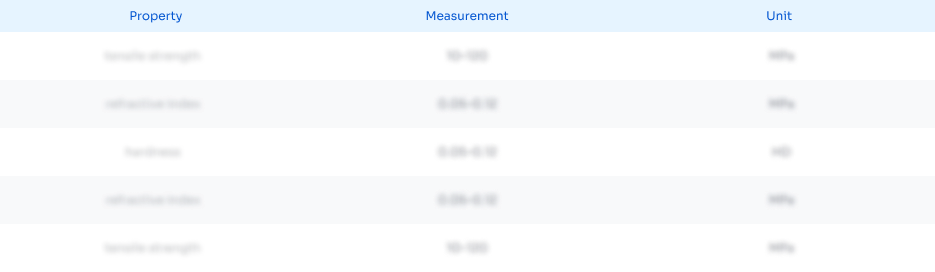
Abstract
Description
Claims
Application Information

- R&D Engineer
- R&D Manager
- IP Professional
- Industry Leading Data Capabilities
- Powerful AI technology
- Patent DNA Extraction
Browse by: Latest US Patents, China's latest patents, Technical Efficacy Thesaurus, Application Domain, Technology Topic, Popular Technical Reports.
© 2024 PatSnap. All rights reserved.Legal|Privacy policy|Modern Slavery Act Transparency Statement|Sitemap|About US| Contact US: help@patsnap.com