Preparation method of pvc foam fireproof board
A fireproof board and foam technology, applied in chemical instruments and methods, synthetic resin layered products, coatings, etc., can solve problems such as peeling, easy peeling of the cement layer, and performance degradation
- Summary
- Abstract
- Description
- Claims
- Application Information
AI Technical Summary
Problems solved by technology
Method used
Image
Examples
preparation example Construction
[0071] The preparation method of PVC foam fireproof board of the present invention, it comprises the steps:
[0072] Provide a foam substrate, place the foam substrate on a sander for sanding, and then remove the dust on the surface of the foam substrate;
[0073] Sanded and dusted foam substrates are stacked together;
[0074] The two surfaces of the foam substrate are respectively coated with a resin for bonding, and the coating amount of the resin is 100g / m 2 -120g / m 2 , wait for the resin to dry automatically for 2min-5min;
[0075] A layer of fireproof layer is covered on both sides of the foam substrate to form an intermediate product;
[0076] Stack multiple above-mentioned intermediate products together, and naturally press for 2min-30min;
[0077] The intermediate product is placed in a cold press for cold pressing, wherein the pressure of the cold press is 1.0kg / cm 2 -1.6kg / cm 2 , the temperature is 35°C-50°C, and the pressing time is 5h-6h;
[0078] Place th...
Embodiment 1
[0106] The preparation method of the PVC foam fireproof board described in the present embodiment comprises the following steps:
[0107] Provide the following components by weight: 20 parts of PVC, 40 parts of phenolic resin, 40 parts of bisphenol F glycidyl ether epoxy resin, 7 parts of polyamide, 10 parts of plasticizer, 8 parts of foaming agent, flame retardant 6 parts of agent, 10 parts of foam regulator. Mix and stir the above-mentioned PVC, phenolic resin, bisphenol F glycidyl ether epoxy resin, polyamide, and foaming agent at a temperature of 30°C-60°C at a stirring speed of 500r / min-1000r / min, stirring After 20min-60min, add plasticizer, flame retardant and foam regulator, continue to stir, and raise the temperature to 60°C-100°C to foam for 30min-150min to obtain a foam base material.
[0108] The above-mentioned foam substrate is sent into the cabinet 22 of the sanding mechanism 20 by the conveying mechanism 10, and the rotating roller in the cabinet 22 is driven t...
Embodiment 2
[0117] The preparation method of the PVC foam fireproof board described in the present embodiment comprises the following steps:
[0118] Provide the following components by weight: 20 parts of PVC, 30 parts of phenolic resin, 30 parts of bisphenol F glycidyl ether epoxy resin, 3 parts of polyamide, 3 parts of plasticizer, 5 parts of foaming agent, flame retardant 2 parts of agent, 5 parts of foam regulator. Mix and stir the above-mentioned PVC, phenolic resin, bisphenol F glycidyl ether epoxy resin, polyamide, and foaming agent at a temperature of 30°C-60°C at a stirring speed of 500r / min-1000r / min, stirring After 20min-60min, add plasticizer, flame retardant and foam regulator, continue to stir, and raise the temperature to 60°C-100°C to foam for 30min-150min to obtain a foam base material.
[0119] The above-mentioned foam substrate is sent into the cabinet 22 of the sander 20 by the conveying mechanism 10, the rotating roller in the cabinet 22 is driven to rotate by the s...
PUM
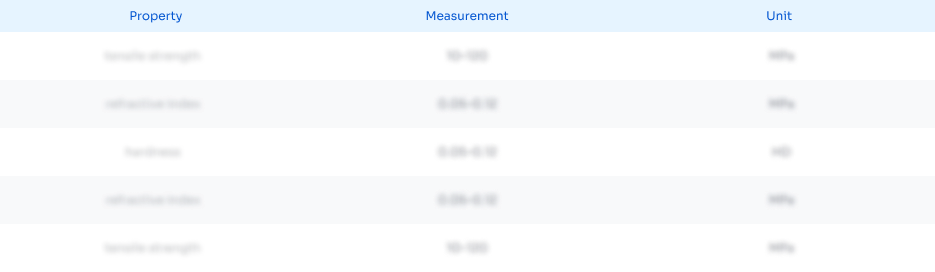
Abstract
Description
Claims
Application Information

- Generate Ideas
- Intellectual Property
- Life Sciences
- Materials
- Tech Scout
- Unparalleled Data Quality
- Higher Quality Content
- 60% Fewer Hallucinations
Browse by: Latest US Patents, China's latest patents, Technical Efficacy Thesaurus, Application Domain, Technology Topic, Popular Technical Reports.
© 2025 PatSnap. All rights reserved.Legal|Privacy policy|Modern Slavery Act Transparency Statement|Sitemap|About US| Contact US: help@patsnap.com