Inverse LED chip and manufacturing method thereof
A technology of LED chip and manufacturing method, which is applied in the direction of electrical components, circuits, semiconductor devices, etc., can solve the problems of packaging yield loss, difficult soldering, and light efficiency per unit area to be improved, so as to improve simplicity and improve packaging yield Effect
- Summary
- Abstract
- Description
- Claims
- Application Information
AI Technical Summary
Problems solved by technology
Method used
Image
Examples
Embodiment Construction
[0045] It can be seen from the background technology that the P and N electrodes of the existing flip-chip LED chip structure are usually on the same side of the chip, so the requirements for packaging technology are relatively high, which may easily cause the loss of packaging yield.
[0046] Although there are a few companies whose flip-chip product designs can realize the distribution of P and N electrodes on both sides of the chip, their designs use the method of connecting the N electrodes to the substrate through through holes, resulting in low packaging yield. In addition, the light output area lost by the LED chip is relatively large, and the area of the high-reflection mirror surface is small, resulting in a decrease in light efficiency per unit area. Therefore, the packaging yield of existing flip-chip LED chips is low, and there is still room for improvement in light efficiency per unit area.
[0047] Therefore, the present invention provides a new flip-chip LED c...
PUM
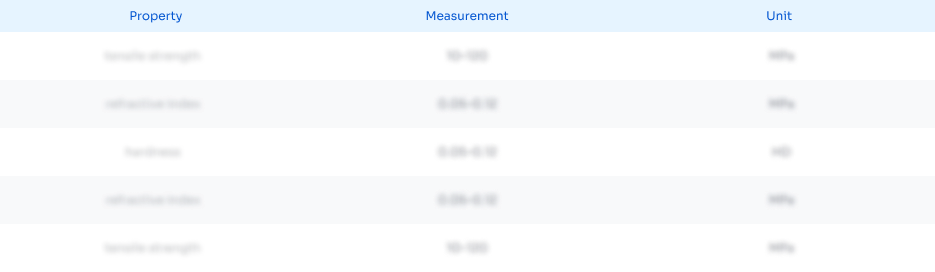
Abstract
Description
Claims
Application Information

- Generate Ideas
- Intellectual Property
- Life Sciences
- Materials
- Tech Scout
- Unparalleled Data Quality
- Higher Quality Content
- 60% Fewer Hallucinations
Browse by: Latest US Patents, China's latest patents, Technical Efficacy Thesaurus, Application Domain, Technology Topic, Popular Technical Reports.
© 2025 PatSnap. All rights reserved.Legal|Privacy policy|Modern Slavery Act Transparency Statement|Sitemap|About US| Contact US: help@patsnap.com