Injection molding machine and injection screw thereof
A molding machine and screw technology, which is applied in the field of injection molding machine and its injection screw, can solve the problems of not being able to obtain excellent comprehensive performance, and achieve the effects of preventing uncontrolled temperature rise, high plasticizing efficiency, and low shear volume
- Summary
- Abstract
- Description
- Claims
- Application Information
AI Technical Summary
Problems solved by technology
Method used
Image
Examples
Embodiment Construction
[0038] In order to further illustrate the principle and structure of the present invention, preferred embodiments of the present invention will now be described in detail with reference to the accompanying drawings.
[0039] refer to Figure 7 to Figure 12 , the present invention provides an injection molding machine 100, which includes a plastic injection part 1, the plastic injection part 1 includes a barrel set 2, the barrel set 2 includes an injection screw 3, and the injection screw 3 is used to inject plastic Plasticized into a melt in the injection molding machine 100 . One end of the injection screw 3 is connected with the drive motor 8 through the transmission part 9, and the other end is equipped with three small parts of the check valve, which include the screw head 4, the non-return ring 5 and the thrust washer 6.
[0040] The injection screw 3 includes a threaded portion 31 and a coupling portion 32 connected to each other. The coupling part 32 includes a coupli...
PUM
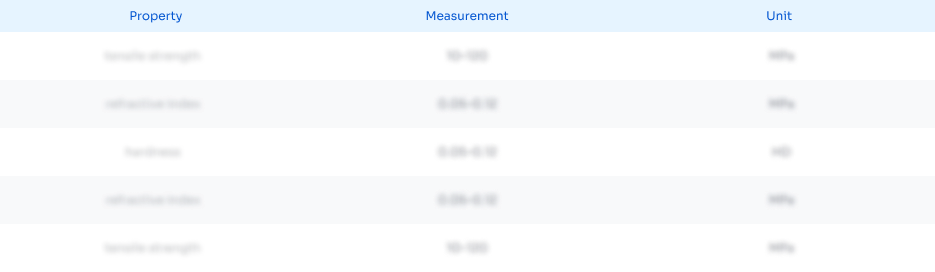
Abstract
Description
Claims
Application Information

- R&D
- Intellectual Property
- Life Sciences
- Materials
- Tech Scout
- Unparalleled Data Quality
- Higher Quality Content
- 60% Fewer Hallucinations
Browse by: Latest US Patents, China's latest patents, Technical Efficacy Thesaurus, Application Domain, Technology Topic, Popular Technical Reports.
© 2025 PatSnap. All rights reserved.Legal|Privacy policy|Modern Slavery Act Transparency Statement|Sitemap|About US| Contact US: help@patsnap.com