Measurement and control method in suspension pouring construction process of continuous rigid frame bridge
A measurement and control method and technology for rigid-frame bridges, applied in special data processing applications, instruments, electrical digital data processing, etc. question
- Summary
- Abstract
- Description
- Claims
- Application Information
AI Technical Summary
Problems solved by technology
Method used
Image
Examples
Embodiment Construction
[0035] The steps of the inventive method are as follows:
[0036] attached image 3 Among them, 1 and 6 are weight beam sections to be identified, 2, 3, 4, and 5 are four measuring points, 9 is a data testing and analysis system, and 7 and 8 are stiffness beam sections to be identified.
[0037] (I) Test the frequency spectrum data of the four measurement points 2, 3, 4, and 5 before the pouring of the weight beam sections 1 and 6 to be identified, and obtain the first-order frequency and mode shape eigenvalues. Through these six parameters, the least square method is used to obtain the comprehensive stiffness EI of stiffness 7 and 8 to be identified 1 and EI 2 (Note: The mass per unit length has been accurately identified in the previous cantilever construction).
[0038] (II) Test the frequency spectrum data of the four measurement points 2, 3, 4, and 5 after the pouring of the weight beam sections 1 and 6 to be identified, and obtain the first-order frequency and mode sh...
PUM
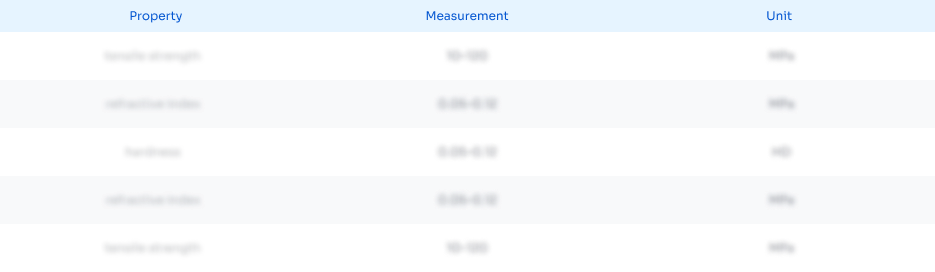
Abstract
Description
Claims
Application Information

- R&D Engineer
- R&D Manager
- IP Professional
- Industry Leading Data Capabilities
- Powerful AI technology
- Patent DNA Extraction
Browse by: Latest US Patents, China's latest patents, Technical Efficacy Thesaurus, Application Domain, Technology Topic, Popular Technical Reports.
© 2024 PatSnap. All rights reserved.Legal|Privacy policy|Modern Slavery Act Transparency Statement|Sitemap|About US| Contact US: help@patsnap.com